张雯娟 1,2,3,4,陈庆祥 1,高 浩 1,2,3,4,魏 剑 1,2,3,4
1.三明学院 机电工程学院,福建 三明 365004 ;
2.机械现代设计制造技术福建省高校工程研究中心,福建 三明,365004;
3.绿色铸锻及高端部件协同创新中心,福建 三明,365004;
4.福建省铸锻零部件工程技术研究中心,福建 三明,365004
摘要:采用 Moldflow 软件对医疗无影灯外壳注射模具的注塑成型过程进行模拟仿真,通过注塑流动情况分析出 制件的最佳浇 口位置,预测和显示气穴、熔接痕等缺陷位置;结合塑件注射压力和锁模力的变化情况、填充过程、温度 变化和产品成型质量分析等情况,帮助工艺人员在试模前找出缺陷产生原因,以此改进模具结构设计和产品结构,从而提高试模成功率 。
关键词:Moldflow;医疗无影灯外壳;注塑模具;成型分析
Moldflow 注射模流分析软件能够很好地验证和优化塑料零部件、注射模具和注射成型流程,能 够有效预防注射产品的各种缺陷,出现问题能够精确分析缺陷原因,提供快速、高效的解决方案,为塑件模拟分析提供强大的支撑[1-4] 。该软件是美国 MOLDFLOW 公司的产品,自1976年发行了世界上第一套塑料注塑成型流动分析软件以来,一直主导塑料成型 CAE(计算机辅助工程)软件市场。利用这种技术手段,以塑料材料流变学及传热学为基础,通过计算机辅助分析,对注塑过程进行数字化、动态化模拟[5],可以对塑料制件过程的各参数进行调整、比较和优化,从而确定最优注塑解决方案。
医疗无影灯作为手术照明灯具,对其外壳要求具有成型质量高 、冷热变形性小 、密度低和电气 性能良好等特性。和普通塑料制件相比,要求设计时尽可能消除阴影,并在长时间的连续工作过程 中,温度不能过高,其成型的技术难点主要在光学性能要求方面,其关键是如何成型出具有较低光 学畸变和低角偏差的光学制品[6],常用的方法有注射成型和注射压缩成型。因此基于这些性能要求 和难点,有必要对该塑件的注塑过程进行模拟仿真及工艺参数优化。本文运用 Moldflow 2018 版对医 疗无影灯外壳进行数值模拟仿真, 分析其注塑成型过程,通过方案对比优化浇口位置以及浇注系统、冷却系统设计,对参数进行优化,获得较小的翘曲变形和体积收缩率,从而满足塑件装配要求和 外观质量要求,解决光学折射率对体积收缩率 、热变形等问题的影响,为指导医疗无影灯外壳部件 的实际生产提供一定的理论依据。
1 塑件结构工艺分析
无影灯外壳结构是外形为 90 mm,内孔为40 mm的圆形件,壁厚 t=4 mm,要求塑件表面质量高、光亮整洁,不能出现拉伤、断裂、料纹等注塑工艺缺陷。涉及到后期该外壳与其他零件组装,注塑成型中不能出现变形或冷缩 。塑件三维模型如图 1 所示。选用 ABS 材料,结合其综合力学性能好、具有高韧性等力学特点,可通过注塑加工成型[7]。
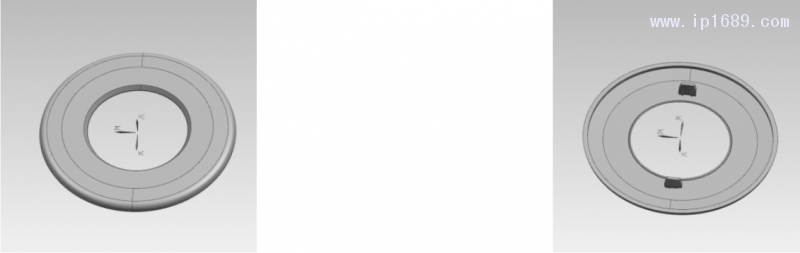
(a)外壁结构 (b)内壁结构
图 1 医疗无影灯外壳三维模型图
2 注塑模流设计及流动分析
2.1 模流分析设置及浇口位置确定
设置模流分析参数:模具表面温 度为 60 ℃,熔体温度为 235 ℃,模具温度范围设定 在 40~80 ℃ 区 间,顶出温度为 89 ℃, 最大剪切应力为0.3 MPa,如图2所示。
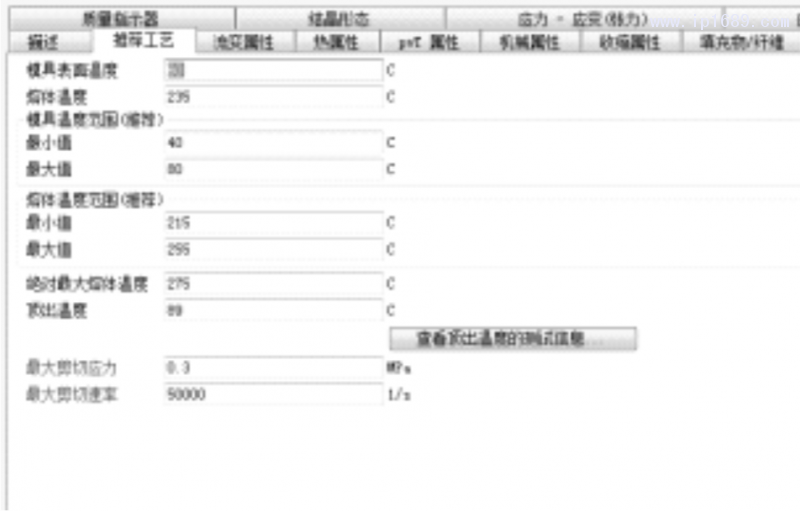
图 2 模流分析的参数设置
无影灯外壳属于薄壳类零件,选 用双 层面网格划分, 纵横比最 大为7.37,最小为 1.16,平均 1.77,其值小 于 10, 匹配百 分比为 85.7%, 自由边、多重边、相交单元等参数都为0,因此模型网格质量良好,满足模流分析要求,有限元模型如图 3 所示。
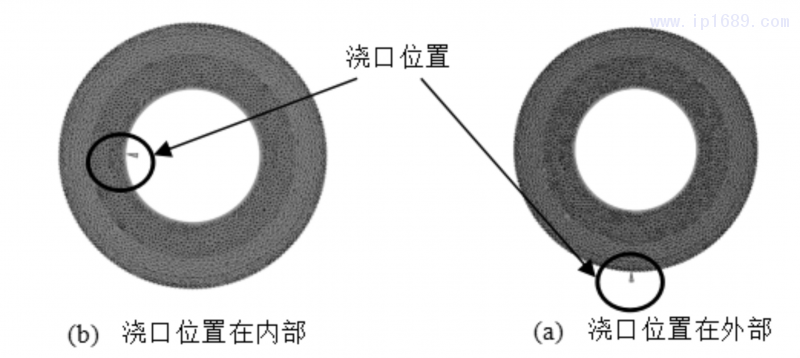
图 3 有限元模型
研究通过设置不同浇口位置模拟塑料填充状态及考虑模具制造经济性的方式来确定最佳浇注方案。方案 1 的浇口位置选择塑件注塑内部,方案 2 的浇口位置设置塑件外部(小三角为浇口注塑位置, 如图 3 所示)。 分析两种情况下的填充时间 、注塑压力、塑件变形及气穴数等参数,如表 1 所示。
表 1 浇口位置方案的分析结果对比
方案 浇口位置 填充时间/s 注塑压力/MPa 变形量 冷凝时间/s 气穴
方案 1 内部浇注 1.221 22.06 0.4397 18.61 多
方案 2 外部浇注 1.216 23.56 0.3890 17.10 少
由表 1 分析对比可确定,方案 2 填充时间较短,注塑压力大,塑件变形量小,冷凝时间短,产生 的气穴少,故选用方案 2 外部浇注进行注塑模流过程仿真,模拟分析采用一模两件模式。
2.2 浇注系统设计
模具浇口设置是影响注塑过程的一个重要因素,最优浇注系统能够有效地减少模具生产周期, 提高生产效率 。 研究采用生产中常用的冷流道浇注系统设计方案,设置潜伏浇口,潜伏浇口具有 自 动拉断 、不影响塑件外观和加工方便等优点,有利于提高生产效率 。其浇注系统设置如图 4 所示。
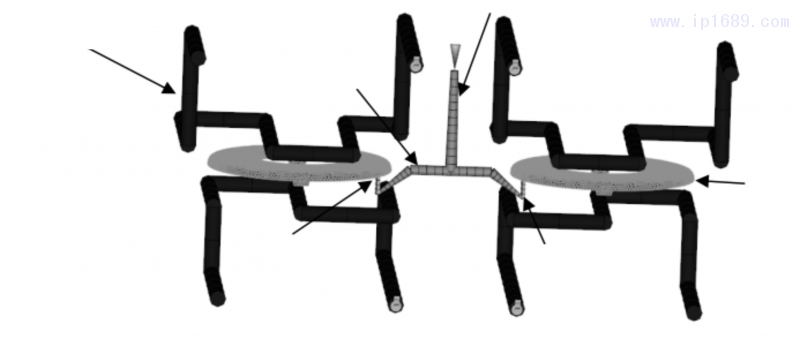
图 4 浇注系统 、冷却系统设计
2.3 冷却系统设计
在注塑过程中,要尽可能地保持冷却系统的高效率工作,使模具型腔表面的温度稳定在一个范围内,冷却系统设计为上、下模 2 条冷却水回路(图4),冷却管道直径为8mm,距离型腔表面 18 mm,设 计时考虑排布位置避开熔接痕的位置。
2.4 流动分析
1.填充时间:由图 5(a~d)可以看出填充过程是对称分布的,注塑流动平衡性较好,填充过程较为均匀。填充时间为 1.471 s,由于塑件尺寸较小,故填充过程顺畅,无注射不足现象。
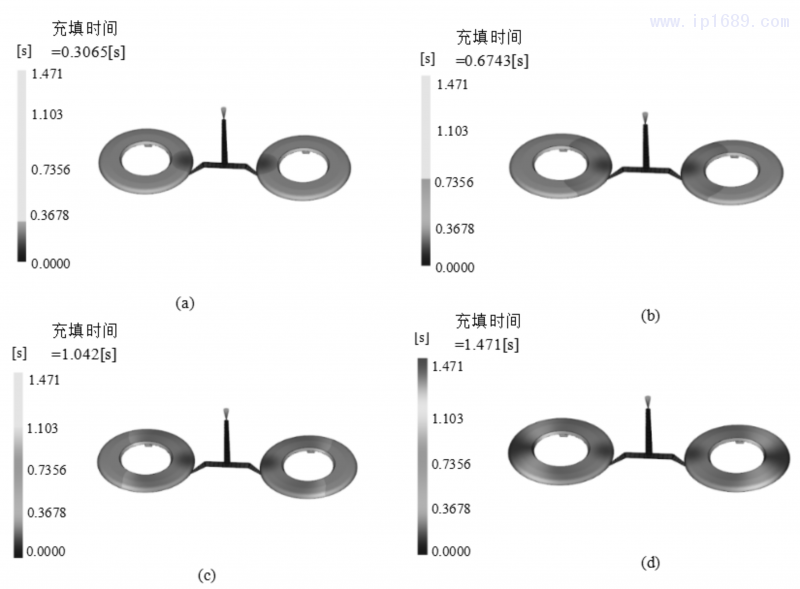
图 5 制件填充过程
2.流动前沿温度:决定熔体充型后是否能混合均匀以决定冷却后的制件质量 。 流动前沿温度最 高为 236.8 ℃,最低为 234.4 ℃,最高温度与最低温度相差 2.4 ℃,变化小于 10 ℃,因此温度分布合 理,反映了该熔体在流动过程中不太可能出现流动阻力大的状况,也无材料分解及低温滞留现象。
3.填充注射压力:整个填充注射压力为 0~44.19 MPa,在 44.19 MPa 时进行 V/P 转换,压力较小,便于注塑,填充压力比较低,不易出飞边,满足生产要求。
4.熔接痕:是指两股料流相遇熔接而产生的表面缺陷[8] 。熔接痕是影响制品质量的重要因素,它的产生会导致制品的强度变低,并且会影响制品的外观。在整个注塑过程中应该避免熔接痕的产 生,如不能避免也应该尽量地使熔接痕处于不易受影响的位置[9]。
由图6可以看出熔接痕主要产生在内孔边缘,此时需在模具上开好排气槽或溢料槽,同 时提高模温,增大熔接痕处的温度,改善熔接痕。
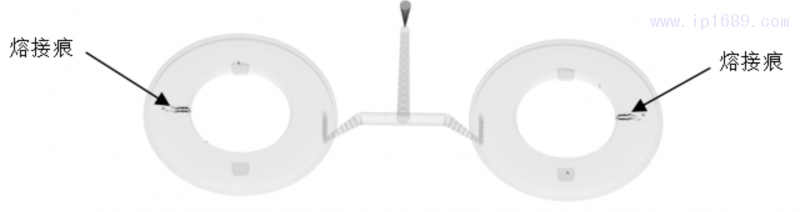
图 6 制品熔接痕位置
5.气穴:主要是型腔内部的空气被熔体包围无法及时排出,这样将会导致制品填充不完整以及保压不充分,同时腔体内的气体被熔体挤压从而产生大量的热量,产品可能因此出现焦痕。如果气穴不能及时排出,将会对产品的质量和性能产生很大的影响。而且气穴越多,制品生产的问题会随之增多,注塑成型质量也会随之降低[10] 。本次塑件注塑气穴位置与熔接痕位置相近,主要分布在内孔边缘,采用排气机构,同时控制注射速度不能太快,不然可能会有烧焦现象,影响产品外观 。
2.5 保压分析
1.注射压力和锁模力:注射节点是观察二维 XY 图的常用节点,通过注射位置压力和锁模力的 XY 图可清晰看出注射压力和锁模力的变化情况。图 7a 显示,在 0~1.443 s 区间,注射压力达到最大值 44.19 MPa,随后注射压力快速下降到 35 MPa,进入稳压注塑阶段。图 7b 显示,注塑成型阶段所需 锁模力在 0~1.881 s 区间快速上升,达到最大值 22.51 t,随着模具开模,锁模力快速下降。
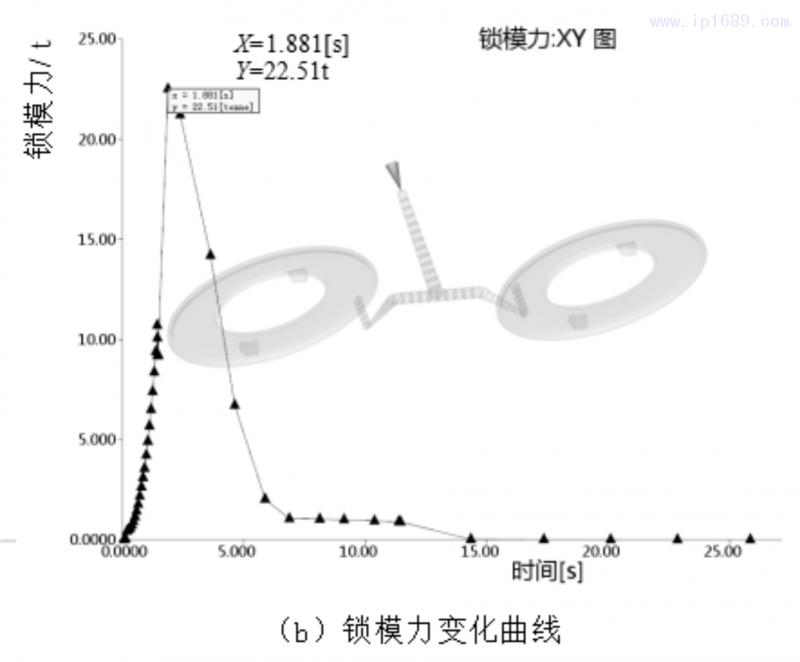
图 7 注塑成型力变化曲线
2.冻结因子:模拟分析可得塑件在 30 s 的冻结因子,即保压结束后的冻结因子为1。整体冻结均匀,能够满足保压补缩,达到顶出要求。
3.达到顶出温度的时间:制件达到顶出的总时间为 39.75 s,模拟分析显示所需塑件顶出温度出现在 15.10 s。为了提高生产效率,缩短生产周期,可将塑件在 15.10 s 时顶出。
2.6 冷却分析
冷却分析是根据塑件在模具中的热传递判断冷却系统的冷却效果,通常冷却系统是用来满足 注射成型工艺对模具温度的要求,并保证塑料熔体的充模和冷却凝固,因此冷却系统的创建是否合 理会影响塑件的冷却速度及收缩性,进而影响塑件最终的表面质量、尺寸精度和力学性能[11-12] 。
根据2.3 中冷却系统设计,冷却水管道的管壁热传导系数为 1,管道冷却介质为乙二醇水溶液 (乙二醇的质量浓度为 40%~60%)。设置参数后,经过冷却模流仿真分析,得出结果如图 8 所示。
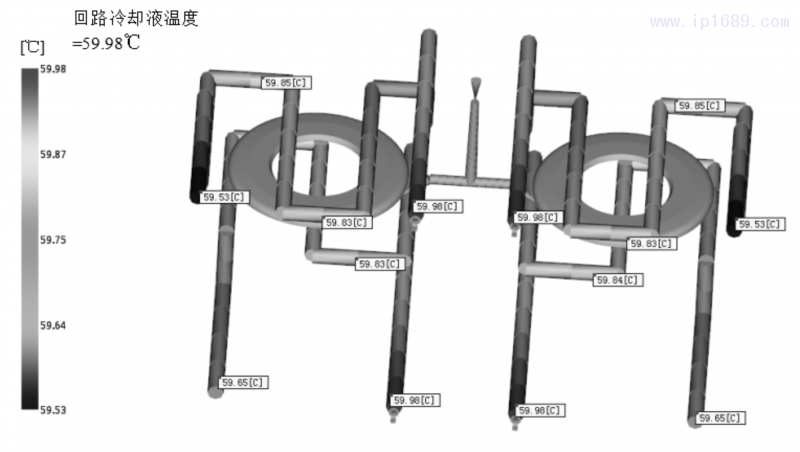
图 8 回路冷却液温度
1.冷却水路的温度变化:图8 显示了冷却液回路的温度变化,冷却液最高温度为 59.98℃,最低 温度为 59.53 ℃,两者温度只相差 0.45 ℃,冷却水路的温度变化差别小,进 、出水口温差控制在 1 ℃ 内,远小于冷却水进出口温度差不宜高于 3 ℃的规定,符合冷却水路的设计要求,同时冷却水路的 长度设计也在合理的范围内 。
2.内外壁温差:图 9a 显示内壁最高温度为 64.79 ℃,最低温度为 63.30 ℃,平均温度为 64.05 ℃; 图 9b 显示外壁最高温度为 63.44 ℃,最低温度为 62.43 ℃,平均温度为 62.94 ℃ 。内外壁平均温差控 制在1.11 ℃左右 。综上所述,冷却管道系统的设计合理,具有良好的冷却效果。
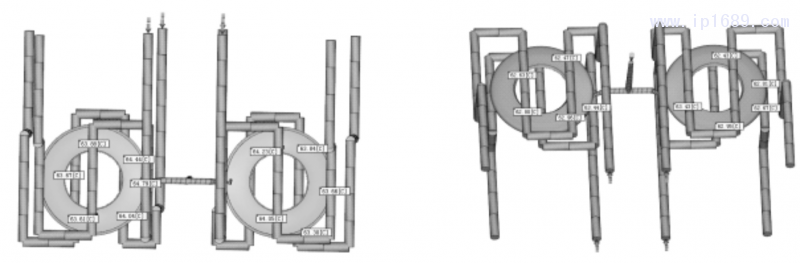
(a)内壁温度分布 (b)外壁温度分布
图 9 内 、外壁温度分布
3 塑件质量分析
3.1 翘曲变形分析
塑件注塑冷却后,取比例因子为 1 时,整体效应变形量最大值为 0.400 7 mm,主要集中在制件 外边缘区域,最小值为 0.116 3 mm,主要集中在内孔边缘区域(图 10a);当冷却不均匀时,制件最大变形量值为 0.013 0 mm,最小变形量为 0.000 3 mm,变形量较小(图 10b);冷却收缩不均匀时,制件最大变形量为 0.407 4 mm,主要集中在塑件外部边缘,最小变形量为 0.135 3 mm,在内孔边缘小部 分区域(图10c);取向效应最大变形为 0.060 3 mm,最小变形为 0.004 6 mm(图 10d)。
由模拟分析可知,当翘曲变形量较小时,若集中在制件外部边缘位置,主要由收缩不均和取向 导致的塑件变形会产生翘曲现象,但整体翘曲变形未超过5 mm 的容差范围,塑件质量是合格的,满足装配要求。对于产品结构设计方面,可以通过改善制件结构及其壁厚等工艺进行优化;对于模具 结构设计方面,可通过修改冷却水路设计或由制件收缩率确定适当的变形比,以期优化注塑模具结 构,减少试模时间,节约成本。
3.2 体积收缩率
图11显示塑件体积与产品尺寸体积的收缩率在 4.125%~5.780% 区间, 平均收缩率控制 在4.953%,收缩变化均匀,制件不易发生变形。最大体积收缩率 10.64%发生在注塑料头处(塑件成型 外),对成型制件质量和注塑生产影响不大。由体积收缩率分析结果可预测制品收缩较严重区域,通过改进模具结构尺寸,弥补制品在冷却脱模后所产生的收缩,如此产品的形状和尺寸就更加符合设 计要求[13]。
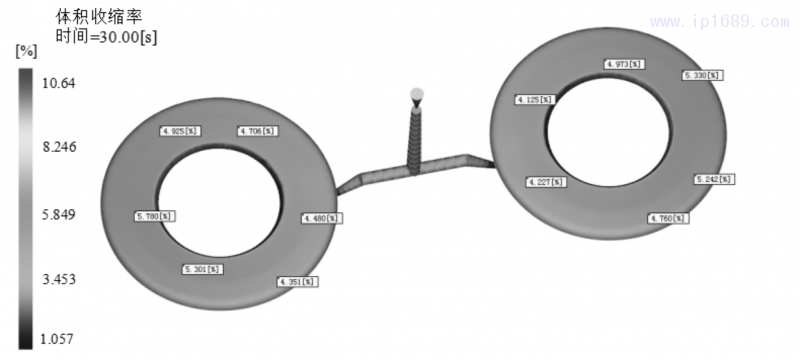
图 11 塑件体积收缩率
4 结论
通过采用 Mold flow 软件,对医疗无影灯外壳进行模流分析,能快速有效地分析注塑最佳浇口位 置,从填充时间 、气穴、翘曲变形分析 、体积收缩率等方面进行分析,预测产生缺陷位置,从而为后期 模具调整结构以及试模提供较为精确的数据依据, 采用外部浇注方案后注塑成型所获得的优化数 据如表 2 所示 。 注塑模拟仿真技术的应用,大大减少了模具修模次数和制造成本。
参考文献:
[1] 王善凯,李晶,胡激涛,等.基于 Moldflow 汽车配件注塑工艺参数优化[J].西安工程大学学报,2015,2(6):692-697. [2] 何建林,白志鹏.基于 Moldflow 的汽车配件 CAE 优化分析[J].机械设计与制造工程,2019,48(2):16-20.
[3] 唐杰,黄荣学,王全亮,等.CAE 技术在汽车灯罩设计中的应用[J].模具工业,2020,46(3):12-17.
[4] 张田荣,曹宏伟.基于 Moldflow 的薄壁壳体注塑件成型质量分析[J].锻压装备与制造技术,2020,55(4):101-104. [5] 修雪颖,汪圣尧,黄兆阁.基于 Moldflow 的注塑阀门应用与仿真[J].现代塑料加工应用,2020,32(5):56-59.
[6] 孙锐,周阳,杜遥雪.基于 Moldflow 的注射成型与注塑压缩成型塑料单透镜仿真对比[J].2016,30(4):52-56. [7] 潘祖仁.高分子化学[M].北京:化学工业 出版社,2010:140-153.
[8] ESSOLES X,TOURNIER C.Automatic polishing process of plastic injection molds on a 5-axis milling center[J]. Journal of Material Processing Technology,2009,209(7):3665-3673.
[9] 徐佩弦.注射制品与模具设计[M].北京:中国轻工业 出版社,2002:124-137.
[10] 陆宝山.注塑缺陷原因分析及改善对策[J].机械制造研究,2009,47(544):25-29.
[11] 黄 海 龙,褚 忠,狄 金 叶.基 于 Imageware 和 Moldflow 的 后 视 镜 逆 向 设 计 与 注 塑 成 型 模 拟 分 析[J].塑 料,2010,39(6):14-16.
[12] 李芳,贾宇霖,黄清刚.基于 Moldflow 的汽车门外板塑件模流分析[J].模具工业,2017,43(8):10-14.
[13] 杨凤霞.注塑制品常见表观缺陷产生原因及其对策[J].塑料,2003(6):59-61.