文/张圆明 黄阔
0 引言
注塑机又名注射成型机或注射机,是将热塑性塑料或热固性塑料利用塑料成型模具制成各种形状的塑料制品的主要成型设备。注塑机能加热塑料,对熔融塑料施加高压,使其射出而充满模具型腔。目前国内很多塑料生产企业还存在大量的全液压驱动系统注塑机,其电机功率恒定,油泵供油量不随注塑过程的流量、压力变化而变化,故产生大量的无效热能、导致了大量电能的浪费,尤其在工艺周期长的保压和冷却阶段,存在很大的节能降本空间。随着电机和控制技术的发展进步,伺服控制技术已逐步在注塑行业得到应用。利用伺服控制技术,具有控制精度高、响应速度快等优点,对传统注塑机进行相应改造,能达到节能30%~70%的效果。广东省某手机配件生产企业通过将注塑机普通油泵电机改造为伺服电机,在节能方面取得了较好的效益,本文对该项目的改造技术方案进行分析。
1 改造项目背景
广东省某手机配件生产企业(以下简称“案例企业”)采用注塑工艺生产的产品为手机塑料配件,平均日产量为37460件。其注塑工艺使用了24台同型号普通注塑机,这些注塑机主要由注射系统、合模系统、液压系统、电气控制、加热/冷却、润滑系统和安全监测系统组成。单台注塑机整体电功率为46.1kW(其中油泵电机37kW、水泵电机3.7kW、加热5.4kW),料筒及干燥器功率为4kW,机械手系统功率为12kW。注塑机的各项用能损耗较高,因此,该企业实施了将全部注塑机的普通油泵电机改造为伺服电机控制系统的项目(以下简称“改造项目”),以达到节能、降耗的目的。
2 技术原理
改造前,案例企业的注塑机为普通油泵电机驱动,其特点为即使机台停止动作,电机仍然不停运作;而伺服注塑机特点为,用相应的功率来为每个不同的动作提供动力,如机台不动,伺服电机则会完全停止。此外,普通油泵电机为普通传动带动系统,能耗高、调控水平低,不能满足注塑工艺节能要求;而实施伺服电机驱动的自动控制系统改造,能够更精确地控制电机的传动方式,提高传动效率、提升功率因数,节约电能,降低生产成本。因此,改造项目实施非常有必要。
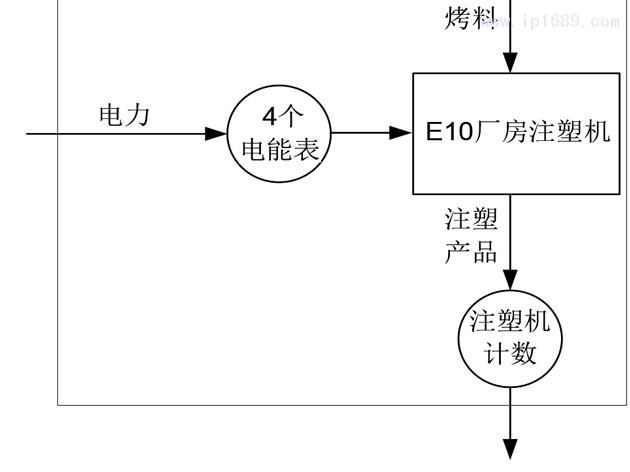
伺服注塑机的动力系统分为伺服电机、伺服驱动器、编码器、齿轮泵、压力传感器和驱动控制模块6个模块,其中驱动控制模块是使伺服注塑机的效能优于传统注塑机的关键模块。伺服动力系统是由伺服驱动器接收驱动控制模块发出的流量、压力指令,转换为转速指令发送给伺服电机;伺服电机带动齿轮泵旋转并输出流量、压力,而压力传感器采集系统压力数据并反馈至伺服驱动器,伺服电机则将转速信息反馈给伺服驱动器;伺服驱动器通过转换将实际的流量和压力信息反馈给驱动控制模块,通过比对实际流量、压力与指令流量、压力的偏差,驱动控制模块再调整指令流量、压力,实现闭环控制,达到工艺要求。
伺服控制系统能按预定要求自动反馈控制注塑装置的机械运动,其控制量是注塑机的机械位移、位移速度或加速度,能使输出的位移准确跟踪输入的位移;液压伺服控制系统则以电机驱动液压泵,将液压泵的机械运动转化为压力推进液压油,再控制各个阀门改变液压油流向,从而推动液压缸作出不同方向和行程的动作,满足注塑机各种动作需求。伺服电机作为执行元件,根据输入电压信号控制其转子转速、转矩并驱动控制对象,具有控制速度快、控制精度高、机电时间常数小、线性度高等特性,因此,应用液压伺服控制系统能够达到良好的自动控制效果,有效节约注塑机各部件运转的能源损耗。
实施伺服控制系统改造后,注塑机将实现以下优化目标:
(1)响应速度快。
注塑机液压系统运行过程中,不同动作所需的流量和压力不一样,液压系统的响应速度对注塑机高效运行非常关键。伺服控制系统响应速度快,流量和压力上升时间快至36 ms,提高了液压系统的响应速度,减少了各动作的切换时间,提升了整机的运行效率。
(2)控制能力强。
普通异步电机定量泵系统因电网电压、频率等波动,引起转速变化,进而引起流量变化,最终导致注塑产品质量降低。而伺服系统控制能力强,可完全按照上位机设定的任意流量、压力曲线运行,易于开发各种塑料产品的成型工艺;闭环油压和转速控制模式下系统压力稳定,波动值小于±0.05MPa,压力控制精度为±1bar,流量控制精度为±0.5%FS,注塑重复精度高,产品一致性好,塑料制品的成型质量高(外观、尺寸及单重)。
(3)能源效率高。
注塑机在预塑、合模、射胶等工艺过程中,动作快慢不一样,即需求的流量不同,而普通定量泵系统的定频电机以一个恒定的额定速度运行,会造成很多时候流量和能量的浪费。液压伺服控制系统的压力、流量采用双闭环控制,在高流量工作阶段油泵电机按照设定的转速运行,在保压、冷却等低流量工作阶段降低电机转速,避免了高压溢流产生的高能耗,大大降低能量浪费,电机运行能耗可降低30%~80%。
(4)维护成本低。
伺服电机与油泵通过无间隙连轴器连接,方便油泵的维护、更换;电机热量难以传导到油泵,降低了油温,提高了注塑机的油封寿命,延长了液压油老化时间,从而节省了注塑机维护费用;伺服电机可配套螺杆泵、柱塞泵、内啮合齿轮泵等,方便生产不同塑料产品时进行配套。
(5)使用方便。
伺服自动控制系统采用双闭环的形式使得液压系统根据设备部件的需求进行供油控制,因此在对电机进行改造时不改变原有使用习惯,只需从上位机取压力和流量信号进行双闭环控制。为方便调试和批量烧写,伺服系统具有电机参数打包、记忆功能,调试界面简单,可调参数少,操作简单、人性化,可通过参数设定选择两种控制模式即工艺模式或速度模式运行,实现多泵并联控制,可控制16个泵、3种工作方式(多泵、复合、多模式)。
3 节能效益分析
3.1 改造项目边界的选取
改造项目位于案例企业E10厂房,改造工作于2019年4月至6月间完成,改造后的电机系统已经投入使用,运转正常。共对24台同型号、生产同类产品的注塑机进行了相同技术的节能改造。在E10厂房安装了4个电能表对24台注塑机进行电量计量,没有对每一台注塑机单独安装电表计量电量。为便于节能量的计算,改造项目边界条件选择E10厂房全部24台注塑机,改造前后项目边界不变,如图1所示。
为了准确计算项目节能效果,改造前基期选择2018年4月~2019年3月,通过对24台注塑机的注塑产品产量和耗电量计量统计,计算出改造前的单位产品能耗;改造后对比期为2019年7月~9月,对24台注塑机的注塑产品产量和耗电量计量统计,计算出改造后的单位产品能耗;最后计算出改造后的年节能量。
3.2 节能量计算方法
根据《节能量测量和验证技术通则》(GB/T 28750—2012)和《节能项目节能量审核指南》(发改环资〔2008〕704号),改造项目节能量等于项目边界范围内各产品(工序)达成的节能量之和扣减能耗泄漏。改造项目范围内产品只有手机塑料配件,用能只有注塑机耗电,且没有能耗泄漏,则节能量可通过手机塑料配件单位产品综合能耗的变化及基准产量计算得到。步骤如下:
(1)计算改造项目边界内塑料配件的基准综合能耗,即统计技术改造前1年项目边界内的电能消耗量,汇总折算成标准煤量。
(2)计算改造项目边界内塑料配件的基准产量,即统计技术改造前1年项目边界内相关生产系统产出的塑料配件数量。
(3)计算改造项目边界内的基准单耗,用技术改造前1年项目边界范围内的塑料配件基准综合能耗除以基准产量,计算出塑料配件基准单耗。
(4)计算技术改造完成后项目边界内综合能耗、产量和单耗。按照步骤(1)~(3)计算方法,统计、计算出技术改造完成后一定时期内(取3个月)的塑料配件综合能耗、产量和单耗。
(5)核算改造项目节能量,即节能量 =(技术改造前塑料配件单耗-技术改造后塑料配件单耗)×改造前1年塑料配件基准产量。
3.3 改造前后的产品产量、综合能耗
(1)产品产量
案例企业实施电机技术改造前后,产品种类均为注塑塑料件,注塑机自动对塑料件件数进行测量统计,企业每天对塑料件产量进行统计,并实施月报制度。具体如表1所示。
(2)综合能耗
案例企业实施电机技术改造前后能源消费种类不变,都为电力,企业每天对E10厂房注塑机用电量进行统计,并实施月报制度。具体如表2所示。
3.4 节能量计算
改造前单耗计算:2018年4月至2019年3月,根据统计数据,改造项目边界范围内塑料件产量为13674448件,注塑机耗电量为3266059kW·h,单位产品电耗为0.2388kW·h/件。
改造后单耗计算:2019年7月~9月,改造项目边界范围内塑料件产量为8330273件,注塑机耗电量为767385kW·h,单位产品电耗为0.09212kW·h/件。则改造后节能率为61.4%,节能效果显著。
节能量 =(改造前单耗 – 改造后单耗)×改造前1年基准产量
=(0.2388 – 0.09212)kW·h/件×13674448 件
= 2006368kW·h
= 200.637万kW·h× 3.013 tce/万kW·h
= 604.5tce
此处电力等价折标系数取2017年度广东省发电标准煤耗3.013tce/万kW·h则项目节能量为604.5tce。
3.5 社会经济效益分析
综上可知,改造项目完成可为企业节电200.64万kw.h/年,按电力单价0.8元/tce计算,可为企业减少能源使用费用160.5万元/年。改造项目总共投入135.8万元,则其静态投资回报期为0.846年,项目经济可行。改造项目实施后,年节能量为604.5tce,年减少二氧化碳排放1279.9t(广东电网平均二氧化碳排放因子为6.379t二氧化碳/万kW·h)。
4 结论
案例企业将24台注塑机的普通油泵电机改造为伺服电机,改造前为普通油泵电机传动带动系统,能耗高、调控水平低,不能满足注塑工艺节能要求;改造后为伺服控制系统,能对注塑机的机械运动按预定要求进行自动控制,使输出的机械位移准确地跟踪输入的位移,从而能够更精确地控制电机的传动方式,提高传动效率,节约电能,降低生产成本。项目实施可为企业节电200.64万kw.h/年,折合节约604.5tec/年,减少能耗成本160.5万元/年,静态投资回报期少于1年,项目经济可行。改造项目完成投入使用后,案例企业节能减排效益显著,综合能源消费量、SO2排放量和CO2排放量都得到一定程度的降低。