魏清兰
( 漳州职业技术学院 机械工程学院,福建 漳州 363000)
摘要: 以电动牙刷头外壳件为例,运用Moldflow软件,进行冷、热流道浇注方案注塑成型CAE分析,比较填充过程、V/P切换时压力、熔接痕位置及体积收缩率等分析结果,综合优选热流道针阀进浇为最佳浇注方案; 结合CAE分析结果,利用UG软件针对合模精度,提出模具优化设计要点,进一步提高模具的合模精度,有效地提高制件的生产质量。
关键词: 外壳件; CAE; 热流道; 精度; 优化
随着产品结构的复杂化和需求的高品质化,塑料制品的生产要求也越来越高。热流道针阀式浇注系统对提高注塑制品的外观质量有着明显的作用。采用热流道针阀式浇注系统生产的制品表面不会留下进浇残痕,可加快型腔填充,并进一步降低注塑压力,减小产品变形,从而获得较高品质的塑件。为了确保塑件注塑的成功率,通常在模具设计前初选不同的工艺方案,应用Moldflow进行CAE分析,预测塑件成型效果。然后,根据产品成型方案比较结果,再对注塑方案进行优化和确认,最终提出合理的成型工艺参数及模具结构设计指导意见。此法可有效提高生产效率,大幅降低模具设计与产品生产的成本[1]。
文章针对某一电动牙刷头外壳体注塑成型进行研究,提出冷、热流道注塑成型方案,并对其进行注塑过程CAE分析,确定出优选方案; 结合CAE分析结果,利用UG软件,进行模具结构优化设计; 并针对中大批量制品生产运用中,对冷热流道方案生产成本比较,得出采用热流道技术的优势。
1 塑件分析
近年来,随着消费水平的不断提高,人们对口腔保健也越来越重视,电动牙刷的使用越来越广泛,对电动牙刷的品质追求也越来越高。“健康”“轻量”“舒适”和“耐用”正成为当下电动牙刷制造工艺发展的主流方向。电动牙刷头外壳件,作为电动牙刷的保护壳和刷毛的护体,要有较好的耐磨性、抗变形、防水性、密封性; 同时,直接与人体口腔接触,健康、舒适又需兼备。因此,制件的品质尤为重要[2,3]。
根据产品质量需求,某公司选用牌号为DURACON(R) M90-44 的POM材料作为牙刷头外壳件的原材料。该材料具有良好的耐磨性、耐反覆冲击性、自润性,且尺寸安定性优,同时又具有较好的握持质感和耐药品性,近年来被广泛应用于牙刷壳体塑件中。
刷头外壳体零件最大外形尺寸为Φ13.3mm×77mm. 塑件前端有若干个形状不一的植毛孔,分别有10°、8°、5°斜孔,另还有5个直角孔。塑件末端内部孔与电动牙刷手柄配合安装,尺寸要求比较高。塑件整体要求表面光亮,不允许有缩水、拉模、变形等注塑不良现象。
2 初选浇注方案
浇注系统的布置、结构和尺寸等设计,对塑件性能、外观及成型难易程度等都有很大影响。考虑到制件的结构及品质的高要求,塑件外表面不留浇口痕迹。结合实际生产,初定采用“冷流道-点浇口、冷流道-潜浇口、热流道-针阀浇口”三种浇注方案。
3 CAE分析结果比较
利用Moldflow对塑件的注塑填充进行对比分析,并通过分析比对选出较优方案。设定该塑件的成型工艺参数为: 模具温度80℃、熔体温度200℃、绝对最大熔体温度200℃、顶出温度143℃,最大剪切速率40000 S-1,最大剪切应力0. 45MPa.以下通过比对填充过程、V/P 切换时压力等几个关键分析结果来确定较优浇注方案。
3. 1 填充过程分析
图1所示为填充过程分析结果。冷流道点浇口进浇方案的填充时间为0. 5259s,冷流道潜浇口进浇方案的填充时间为0. 5275s,热流道针阀浇口进浇方案的填充时间为0. 5126s. 从填充结果看,各浇注方案均能顺利填充,热流道针阀浇口进浇方案的填充时间略短一些,在大批量生产中效果可显见效。
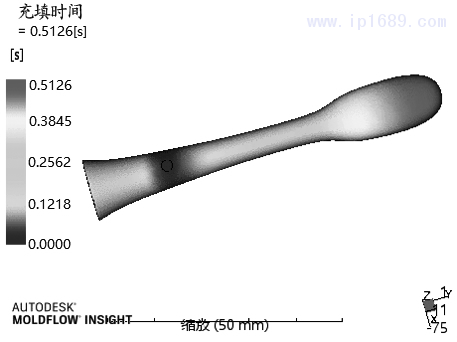
3. 2 V/P切换时压力
V/P ( 速度/压力) 转换显示了注塑过程中压力变化接近压力转换点时型腔所能达到的压力值。图2为三种浇注方案V/P切换时压力分析结果。其中冷流道点浇口进浇方案为112. 2MPa,冷流道潜浇口进浇方案为168. 4MPa,热流道针阀浇口进浇方案为60. 94MPa. 注射压力较低,生产条件容易满足,且流动越平衡[4]。显然热流道针阀浇口进浇方案较好。
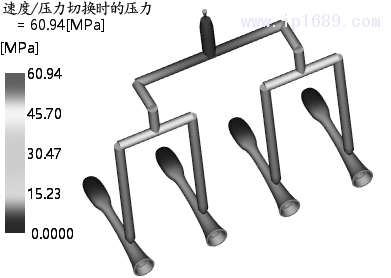
3. 3 熔接线位置分析
塑胶在模腔内的交汇处会产生熔接线。熔接线主要影响塑件的外观,严重时,对制品强度会产生影响。图3所示为三种浇注方案的可能存在的熔接线位置。从分析结果看,冷流道潜浇口进浇因不存在熔体汇合,进浇效果较好,其余两种方案均在图示箭头处存在产生熔接线的可能。
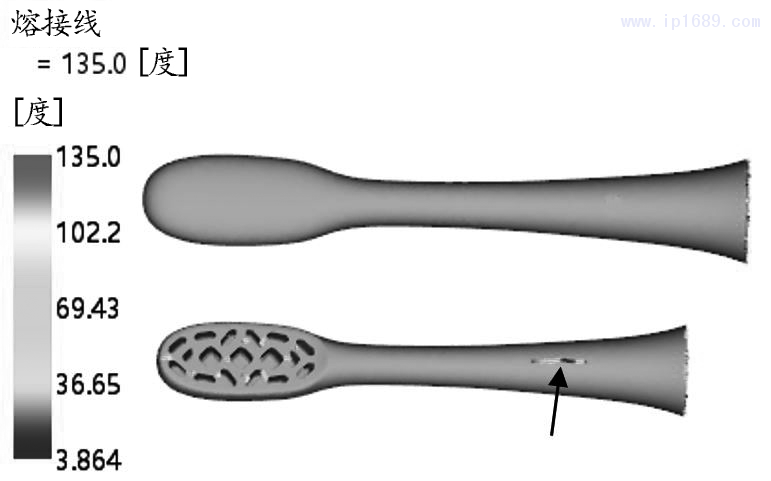
3. 4 平均体积收缩率
平均体积收缩率是半空隙厚度区的体积收缩率平均值,此结果可用来检测模型中的缩痕。从图4所示分析结果看,热流道针阀浇口进浇方案刷头部分,表面收缩均匀,缩水的风险较小。该方案较优。
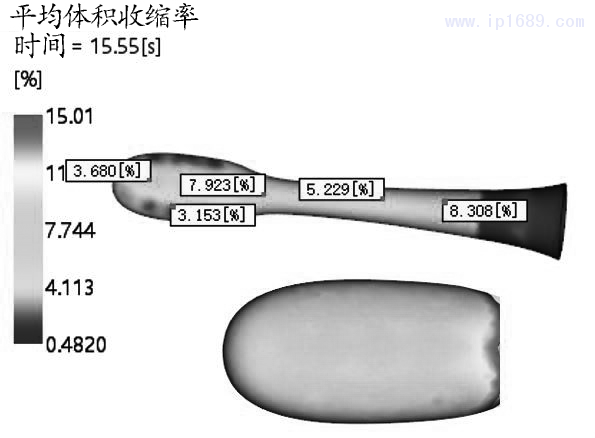
综合上述分析结果,热流道针阀浇口进浇方案要优于其余两种方案,选用该设计方案。针对分析中,热流道针阀浇口进浇方案可能产生的熔接线缺陷,可用增大流速、温度、压力等方法降低熔接线的明显度,以达到表面要求。热流道模具虽然结构较复杂,模具造价大多高于冷流道模具; 但因其不存在流道废料,节省了原材料,在成批量的塑件生产中,塑件生产成本降低得更明显,故选择热流道针阀式浇注方案生产制件合理。
4 模具结构设计要点
依据CAE分析结果,利用UG软件对塑件进行模具结构设计。根据制件的尺寸、生产批量等,模具采用一模四腔,左右对称并列排位。根据分型面的选择原则及制件的外形结构,选择塑件最大投影面积处为分模线位置。因该处在制件注塑成型后会留有合模痕迹,若处理不当,会影响牙刷头的品质。在模具结构设计和模具加工中应尽可能处理好合模痕迹。以下对模具结构设计进行优化以保证合模精度: 因制件外观要求较高,为确保分模线处的合模痕迹尽量减小,以满足制件外观要求,结合实际生产经验,模具设计时,采取了以下几个方法,保证动定模合模精度。一是在图5( a) 所示动模腔箭头所指处增加了管位,其主要目的是为了确保动定模两腔合模精度,尽量减小制件的合模痕迹。二是在模架设计时在模架四个角落分别做了管位,以便提高量产过程中产品合模线接触面的稳定性; 对模架做了0度精定位。三是在模具加工时采用组立加工治具,如图5( b) 所示,对动定模处组立治具放电,抛光,确保分模面加工精度[5]。
根据塑件的结构特点,模具采用哈夫模具结构。成型制件内孔,采用铍铜芯子的侧抽机构。内孔型芯采用铍铜芯子,一方面可以保证成型性,另一方面可以促进散热,以有利于内孔冷却[6]。植毛孔处各孔形状大小不一、特别是孔的斜度不一致,该处采用斜孔镶件,将其安装部分采用 T 形头与底座装配一起,便于更换,且有助于推出制件。
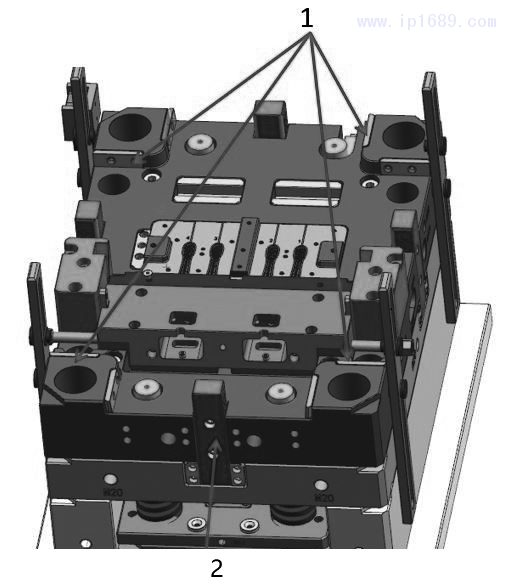
5 生产运用
以上所设计的热流道模具已运用于某公司实际生产中。以10万件生产批量对比冷、热流道方案的生产成本。由模流分析可得冷流道系统每个周期成型4个产品约需70s,而实际生产中采用热流道系统每个周期成型4个产品约仅需50s,一天按22小时算,冷流道一天可以生产4525个产品,约需22. 1天完成该批量生产,热流道一天可以生产6336个产品,仅需15. 8天完成该批量生产,后者生产效率明显高于前者。同时,使用冷流道需增加人工去除浇口,使用热流道则可省去该工艺,实现全自动的快速生产,从而进一步提高生产效率,且省去人工费用。以上两部分生产成本从实际生产情况统计比较,采用热流道可比采用冷流道节省成约25% . 同时,使用热流道系统,每周期可节省流道凝料的原材料13. 6 g,整批次共可节省约340kg,按原材料15元/kg价格计算,可节省5100元,约占生产成本5. 1% . 此外,采用热流道模具,较容易实现型腔流动平衡,还可降低注射压力和锁模力,产品良品率较高。不过,使用热流道模具,其模具成本较高,该热流道模具比冷流道模具增加了约 1. 2万元,约占生产成12% . 经生产企业综合考虑注塑机产能、原材料成本、人工费用和模具成本等因素并进行分析比较,该批量产品采用热流道模具生产比采用冷流道模具生产节省了约18%的成本。综合以上分析,虽然采用热流道会使模具成本增加,但是针对大批量生产,综合考虑生产效率、原材料成本和模具成本等因素,采用热流道技术反而可以降低生产成本[7]。
6 结论
在电动牙刷头外壳件模具结构设计中,结合制件的质量要求,拟定冷流道点浇口进浇、冷流道潜浇口进浇和热流道针阀浇口进浇三种浇注方案,运用Moldflow软件进行注塑过程 CAE分析,通过充填过程、V/P切换时压力、熔接线位置及平均体积收缩等分析结果对比,优选出热流道针阀式为较优的浇注方案。根据CAE分析结果,利用UG软件进行模具结构优化设计,提出解决分模线处注塑痕迹的设计要点。经生产验证,模具生产效率高,制件质量符合技术要求,采用热流道浇注方案节省了约18%的生产成本,已大批量生产。本文可为注塑同类产品的模具设计提供借鉴。
参考文献:
[1]俞蓓.基于Moldflow的汽车配件热流道注塑方案对比[J].重庆科技学院学报( 自然科学版) ,2019,21( 02) : 56 ~ 60 + 104.
[2]梁宁宁.基于Siemens NX的电动牙刷模具抽芯机构的设计与优化[D].济南: 山东大学,2019.
[3]金敦水.电器壳盖的注塑模具设计[J].中原工学院学报,2012,23(01):75~78.
[4]尹小定,赵会娟,王登化,等.注塑模设计中冷、热流道技术在Moldflow中的比较分析[J].吉林化工学院学报,2019,36(09):28~34.
[5]杨双华.后视镜外壳注塑CAE与模具设计[J].塑料科技,2019,47(12):112~119.
[6]樊晓红.汽车音箱面板注射模设计[J].模具制造,2010,10(07):58~59.
[7]陈进武,曹轶杰,苏庆勇.Moldflow在塑料模热流道技术中的应用[J].塑料工业,2014,42(04):31~34.