陈猛1,董岱2,逄鹏博3,梁健民1,胡颖瑜1,李松晶4,*
(1.震德塑料机械有限公司,广东佛山528300;2.南京工业职业技术机械工程学院,江苏南京210023;3.震雄机械(深圳)有限公司,广东深圳518122;4.哈尔滨工业大学机电工程学院,黑龙江哈尔滨150006)
摘要:在全面推进制造业信息化和智能化的背景下,针对注塑产业离散制造现状,开展注塑离散制造过程的自主感知与控制关键技术研究。本文对注塑装备各功能模块的工艺结构进行升级改造,研究大数据运行过程关键数据的自主感知、缺陷在线采集和智能识别、生产任务自组织调度、装备智能控制策略自适应调整和装备上云智能化管理平台,实现生产过程智能化监控、管理、服务和维护的注塑全新工艺,助力大型企业注塑车间无人化作业实现,提高下游产业注塑产品质量,实现塑机装备产品的智能化提升。
关键词:注塑产业;离散制造;智能感知;数据分析和优化;智能控制
制造业是国民经济的物质基础和产业主体,是衡量国民经济发展的重要标志。注塑制造业作为现代社会中工业发展不可或缺的部分,注塑工业的发展水平在一定程度上也代表了一个国家的工业发展水平。注塑行业作为离散型制造的典型代表,其产品在计算机、家电、通信电子、医疗和汽车等领域的应用范围巨大。随着《中国制造2025》的颁布,我国开始全面推进制造业和信息技术的高度融合,以使企业制造过程更加信息化和智能化[1-3]。
随着技术的发展,以高精度化、全自动化、网络化、一体化与复合化为特征的注塑机智能化发展要求日趋紧迫,国内外注塑机系统在物联网、大数据、云制造发展背景下,纷纷加速智能化进程。目前国内注塑机大部分控制系统实时性差、速度慢、控制精度不高、开发周期长、保养维护升级困难。国内注塑机品牌型号众多,生产实时数据难以采集、信息断层,设备利用效率难以有效提高[4-5]。生产过程监控困难,仍通过传统注塑加工和控制工艺改造实现节能降耗,注塑机离散制造过程的智能控制和管理方面的研究还较少。
因此,本文提出对注塑离散制造过程的自主感知与控制关键技术进行研究,将离散制造人工智能系统引入注塑行业,对注塑装备各功能模块的工艺结构进行升级改造,研究大数据运行过程关键数据的自主感知、缺陷在线采集和智能识别、生产任务自组织调度、装备智能控制策略自适应调整和装备上云智能化管理平台,实现生产过程智能化监控、管理、服务和维护的注塑全新工艺,助力大型企业注塑车间实现无人化作业,提高下游产业注塑产品质量,实现塑机装备产品的智能化提升。
1 注塑机离散制造智能感知及控制系统构建
传统注塑制造是典型的离散制造系统,为实现注塑制造过程的智能感知和控制,需对其进行改造升级。本文根据注塑行业智能化发展要求,提出的注塑离散制造过程智能感知与控制系统总体方案如图1所示。首先,该系统提升了注塑装备的自动化智能化性能。其次,为实现该系统功能,搭建了统一信息化平台,实现运行过程关键数据的自主感知、缺陷在线采集、精准定位和智能识别。另外将CPS系统数据集成分析建模,研究成型工艺与参数自适应方法。进而搭建注塑产业多类型生产任务自组织调度、装备智能控制策略自适应调整和装备上云智能化管理平台。最后,建成了生产过程任务组织调度及参数优化配置决策等功能的注塑行业人工智能工业服务系统。
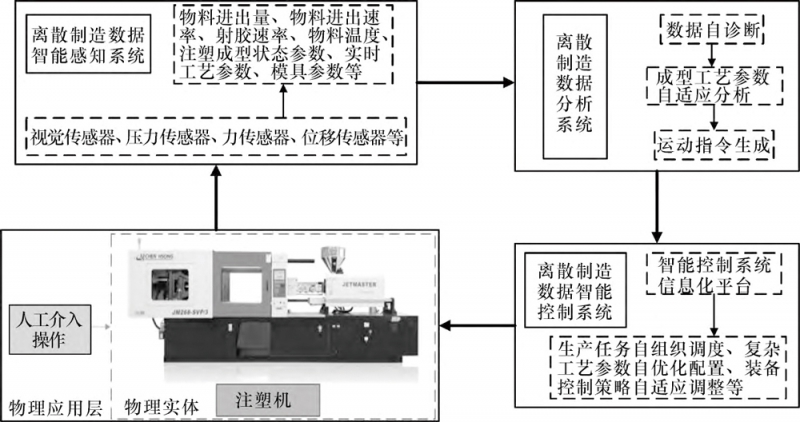
图1注塑机离散制造智能感知及控制系统
本文注塑机系统的智能化感知及控制系统构建重点研究以下几个部分:注塑机本体、锁模机构、射胶机构、动力系统、控制系统、塑化系统和网络通信系统。锁模机构是注塑离散制造装备系统的关键部件,采用有限元应力分析设计优化高刚性锁模部分,设计可调试滑板承托移动模板,镀硬铬高拉力钢连接柱,实现自动模厚及锁模力调整。射胶机构利用高精度传 感器、温控算法和高扭矩液压马达,从而达到减少漏料、提高精度,缩短熔胶时间的目的。动力系统通过优化液压动力装置和伺服驱动系统,实现精确的压力和流量控制,提高注塑机的工作性能和制件的精度。控制系统采用Ai-12高级智能计算机控制器,能提供分段开模、闭模和多段熔胶设置,帮助用户达到最佳熔胶效果。塑化系统零件采用进口材料SDK61,保证其强度和耐磨性。多种螺杆塑化参数供选择,针对不同塑料获得更好的塑化效率和塑化效果。网络通信 系统采用EthercAT技术,支持IPV4、IPV6等技术的工业互联网,可采集并上传设备状态、作业操作、环境情况等数据,并根据远程指令灵活调整设备运行参数。可让厂家通过联网实现远程在线监控,并向客户提供运行维护解决方案。
综合以上研究成果及技术集成创新,推出注塑机MK6e系列产品及MK6.6升级版产品,并以MK6.6升级版注塑机系统为基础,搭建了离散类产品硬件测试实验平台进行研究。
2 基于视觉检测技术注塑件瑕疵实时检测
本文注塑制造过程运行数据的自主感知系统,包含智能化控制系统,可与开发的一站式网络控制系统、MES系统实现远程连接,实现持续改进。建立了高效、安全的智能服务系统,提供的服务能够与产品形成实时、有效互动,大幅度提升嵌入式系统、移动互联网、大数据分析、智能决策支持系统的集成应用水平。主要包括数据采集模块、网络传输模块、数据分析模块、模型构建模块和数据显示模块。
采用视觉检测技术的注塑件瑕疵实时检测系统是注塑制造过程自主感知系统的典型代表。该系统以注 塑生产的零件为对象,对注塑离散制造过程中的产品数据高精度瑕疵样本分析,采用机器视觉检测技术,对生产中产品的瑕疵进行准确定位与瑕疵识别。该技 术原理框图如图2所示。
YOLO全称youonlyLookonce,是一种卷积神经网络YOLO是由JosephRedmon继FasterR-CNN之后提出的,创造性地将候选区和目标检测这两个阶段合二为一,实现了保持高精度的前提下对整张图片和视频的实时检测[6-7]。但是标准YOLOV5n算法无法有效提取困难样例缺角和缺料的情况[8-10],提出改进型YOLOV5n的注塑件瑕疵检测算法,分别对其下采样结构、特征提取模块和检测头进行改进。首先利用最大池化层能凸显纹理特征和平均池化层保留上下文关系、减少无用信息的原理提出了新的下采样结构 Respool和InceptionAB。然后,利用高效长距离网络架构的堆叠模式,结合DenseNet的连接方式把shuffle模块连接在一起,形成了高效长距离shuffle特征提取模块ELSBELSB将浅层特征复用,有效提取瑕疵的边缘特征,并减少参数量和计算量。最后提出了结合SE注意力机制的解耦检测头DCH-SE,有效地提升了回归器和分类器的检测能力,平衡了召回率和准确率算法流程如图3所示当实时关键帧提取算法检测到注塑件中心点坐标接近整个图像的中心时,则判断当前帧为关键帧,然后将关键帧输入到注塑件瑕疵检测算法中。实际检测效果如图4所示,分别采用YOLOV5n基准算法、Respool+ELSB+DCH-SE和InceptionAB+ELSB+DCH-SE算法对开关面板的缩水、缺角和脏点缺陷进行检测,改进后算法的检测效果远好于基准算法。通过以上改进,提升了8.9%的mAP值,使算法兼具计算效率和检测精度。
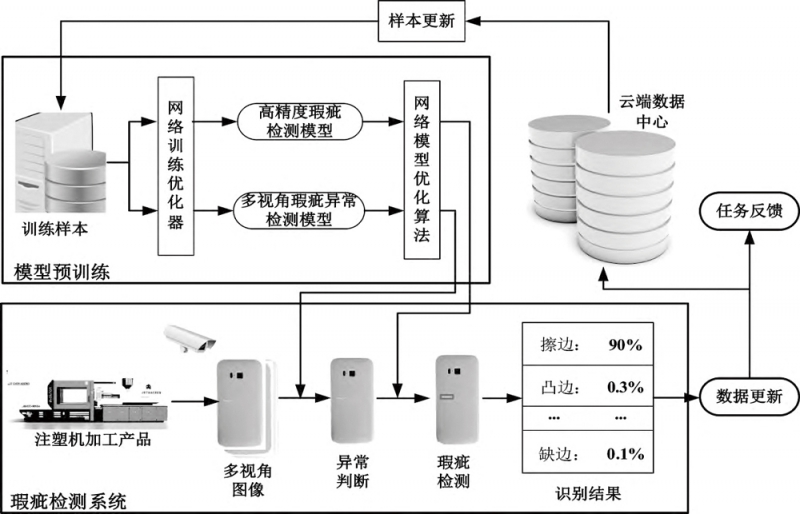
图2注塑产品质量的机器视觉感知技术
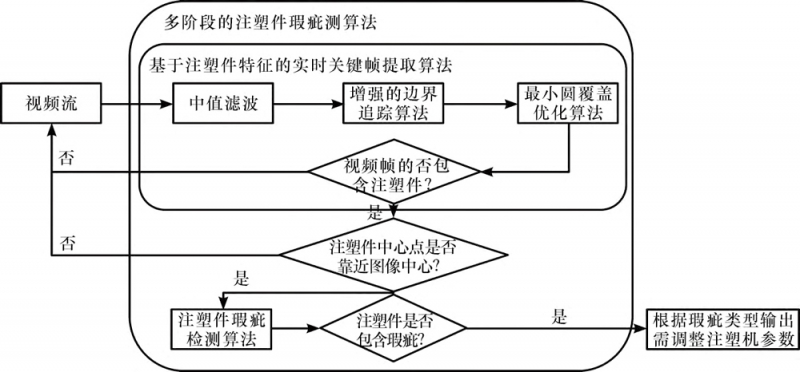
图3算法流程图
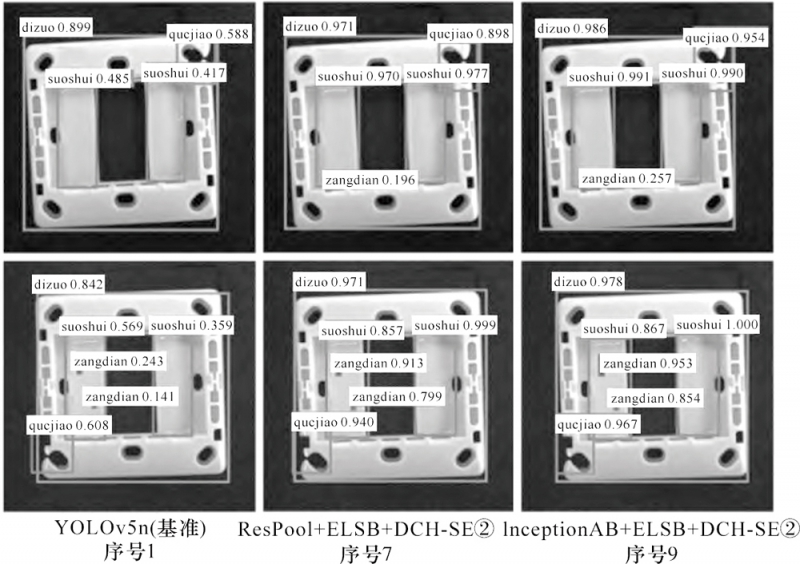
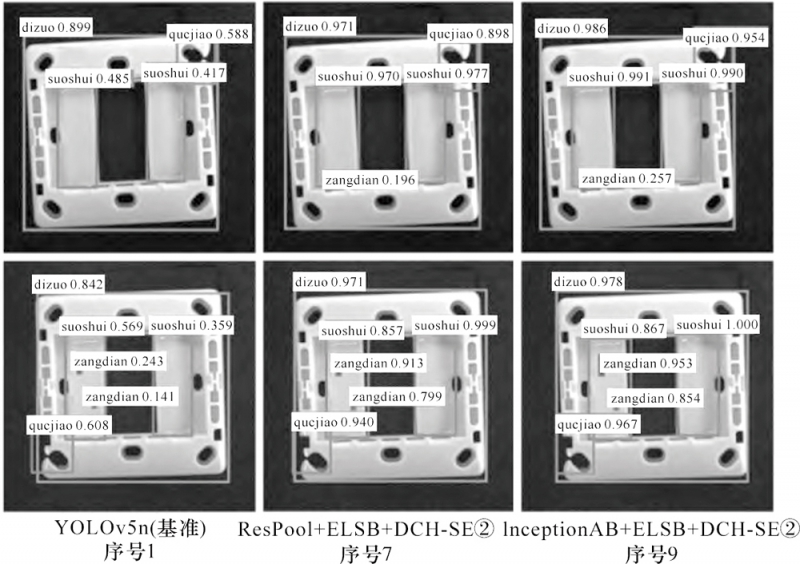
图4瑕疵检测算法效果图
3 注塑机离散制造过程数据分析
通过对注塑离散生产过程的数据特点分析,提出的数据分析与优化过程主要包括装备管理、状态检 测、故障诊断、状态预测、健康评估、保障决策等过程。在注塑离散制造过程中,注塑过程中产生的重要数据包括物料进出量、物料进出速率、射胶速率、物料温度、注塑成型状态参数、实时工艺参数、模具参数等。获取到原始数据后,数据自诊断过程分别利用了数值分析方法(包括拉依达准则和格拉布斯准则)和人工智能方法(深度卷积神经网络)进行分析,处理结果通过数据匹配过程进行进一步筛选,目的是排除异常数据。最后将诊断数据传送至下一环节(成型工艺参数自适应分析),如图5所示。
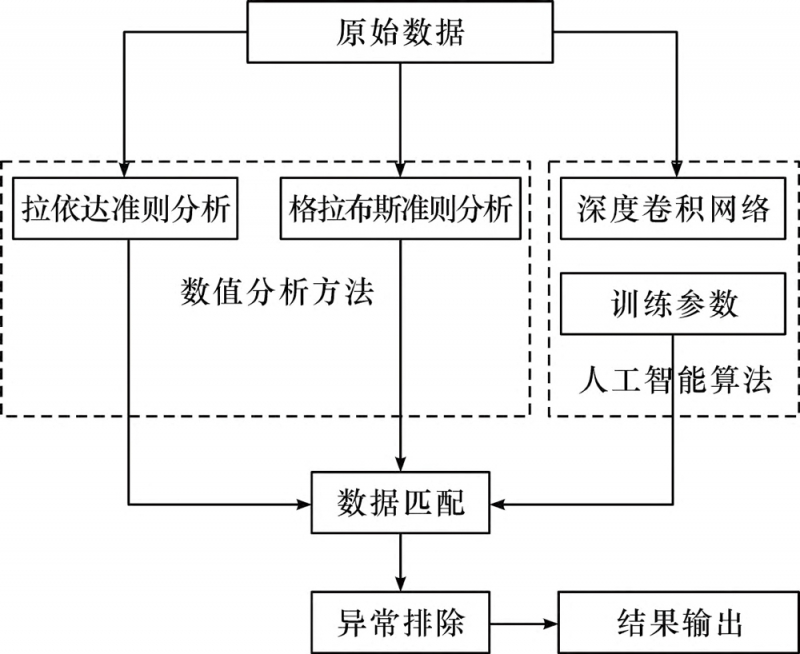
图5数据自诊断过程示意图
注塑离散生产过程中,异常数据将对系统监测和进程造成极大干扰,甚至出现事故。离散分布的工业大数据也将造成控制层主控单元的巨大计算负荷。数据自诊断过程能够有效提出测量环节中因为传感器误差而产生的异常数据,从源头上避免事故。所提出的注塑成型工艺参数自适应分析过程如图6所示。
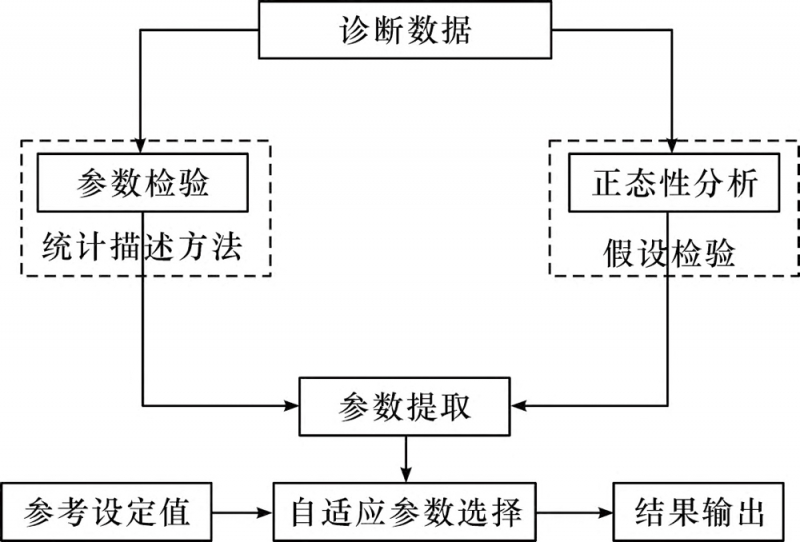
图6成型工艺参数自适应分析过程示意图
自适应调整后的参数数据需要进行数据转换处理,形成运动控制指令,其生成过程如图7所示。其中,注塑机运动学模型和动力学模型是根据注塑机机身物理参数进行建模和设定的,具有不变性。物料状态、注塑状态、取件状态数据反馈的是当前生产线上的实时状态,其主要作用是与自适应参数进行匹配,形成偏差信号。偏差信号在运动控制过程中作为输 入,转化为注塑机能够识别和执行的运动指令,从而精确地执行上料、注塑、取件等指令。
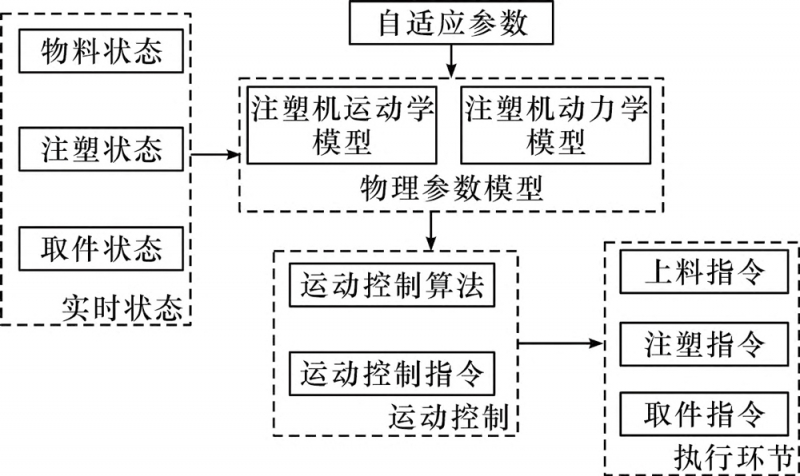
图7运动指令生成环节示意图
4 注塑离散制造过程智能控制
根据系统要求提出的注塑生产线智能控制系统模型主要由锁模机构、射胶机构、动力系统、控制系统、塑化系统等组成。本文注塑机智能控制系统包括注塑产业多类型生产任务自组织调度、复杂工艺参数自优化配置、装备控制策略自适应调整等。为了实现注塑产业离散制造智能感知与控制关键技术的应用,初步搭建统一信息化平台,如图8所示。
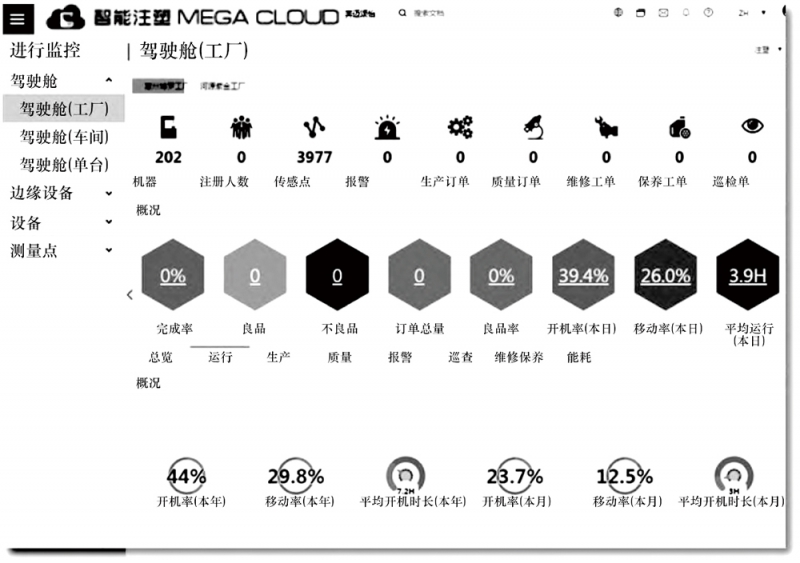
图8智能控制系统统一信息化平台
智能控制系统的智能化实时诊断与决策过程如图9所示(图示为某一指标),该模块包含多项主要参数的显示,包括设定的参考曲线,以及实时数据走势曲线。模块内包含统计性分析与曲线拟合算法,能够精确地反映实时数据。根据统计性分析(如正态分析,参数检验),可计算并显示实时数据与参考曲线的误差,以及系统建议的修正值。
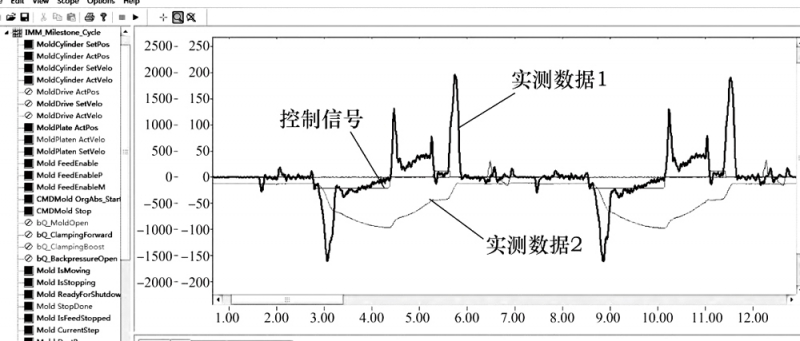
图9智能化实时诊断与决策过程示意图
5 结论
本文对注塑离散制造过程的自主感知与控制关键技术进行了研究,对注塑装备各功能模块的工艺结构进行了升级改造,搭建了硬件测试平台。以开关面板的缺陷瑕疵为主要在线采集检测对象,建立视觉检测系统,改进和优化注塑件缺陷检测的深度学习算法,实现缺陷在线采集、精准定位和智能识别等功能。通过上位机接收视觉检测缺陷信息,结合注塑经验参数,完成智能调参工艺,实现保压切换位置、保压时间、当前模数等注塑参数自主感知与注塑工艺参数自 适应修正。对注塑离散生产过程的数据进行了分析和 优化,研究了数据自诊断,工艺参数自适应分析和运动控制指令生成过程。建立了注塑生产线智能控制系统模型,搭建CPS系统及云平台,初步将智能感知调节程序融入注塑生产。
参考文献
[1]葛妍娇·基于智能感知网的离散制造车间物料配送关键技术研究[D].南京:南京航空航天大学,2023.
[2]曹银平·大数据平台注塑装备行业实现智能化转型的关键[J].自动化博览,2017,34(2):58-60.
[3]吴伟·信息时代下注塑产业的改革与发展[J].石化技术,2018,25(8):205.
[4]陶永亮,姚科·注塑过程控制技术和智能化发展趋势[J].工业控制计算机,2019,32(4):17-20.
[5]何和智,高琦,张涛·国内外大型注塑机技术发展动态综述[J].中国塑料,2022,36(11):140-149.
[6]曾凯,李响,贾建梅,等·基于YOL.ov3-spp的缺陷检测优化模型[J].计算机系统应用,2022,31(2):213219.
[7]刘志文·基于机器视觉的注塑制品缺陷检测研究[D].北京:北京化工大学,2022.
[8]文生平,洪华锋,舒凯翔·精密注塑手机外壳表面缺陷视觉检测系统设计[J].塑料工业,2017,45(9):53-56.
[9]向玉开,雷林建,张悦·基于计算机视觉的注塑零件表面缺陷在线检测研究[J].塑料工业,2019,47(sl):87-90,97.
[10]陈儒侠,任德均,严扎杰,等·基于机器视觉的注塑空瓶缺陷检测系统[J].科技与创新,2018,6(19):13-15.