黄关山1,朱金婷2*
(1.珠海城市职业技术学院新能源学院,广东珠海519090;2.重庆公共运输职业学院,重庆402247)
摘要:通过注塑成型工艺制得汽车引擎盖,所用材料为丙烯腈-丁二烯-苯乙烯三元共聚物(ABS),借助Moldflow软件对其进行模流分析,通过响应面代理模型及遗传算法研究成型过程中熔体温度、模具温度、保压压力以及保压时间对制件缺陷的影响。结果表明:各因素对翘曲变形量的影响顺序为:保压压力>熔体温度>保压时间>模具温度。当制件的保压压力为58MPa、保压时间为20s、模具温度为30℃、熔体温度为230℃时,制件的翘曲变形量最小,优化后制件翘曲变形量较未优化前减小0.1886mm,整体质量提升31.33%。通过遗传算法计算,优化后的预测值为0.40mm,与最终的模拟值相对误差为3.2%,满足实际生产要求。
关键词:汽车引擎盖;响应面代理模型;遗传算法;注塑成型;工艺优化
随着环保轻量化概念的不断兴起,汽车引擎盖已经由传统的铝制钢制材料向塑料材料转变[1]。目前,市面上已经出现由丙烯腈-丁二烯-苯乙烯三元共聚物(ABS)材料制成的塑料引擎盖。ABS具有冲击强度好、耐磨性能优良、热学性能好、不受酸盐影响等优点,因此被广泛应用于机械、电气、纺织、汽车、飞机、轮船等制造工业及化工领域[2]。针对塑料制件在成型过程中存在的缺陷问题,很多学者对其进行研究。卢惠亲等[3]研究汽车塑料内饰件,结合正交试验法,获取一组较佳的工艺组合,减小制件的变形量。刘杰等[4]对某车型的引擎盖进行模态分析及优化,通过有限元分析提高整车的动态感知水平。李沛等[5]通过逆向工程对汽车的引擎盖内板法向变形质量进行分析,对其三维模型进行有限元分析,提升了制件的成型质量。吕玥蒽等[6]基于轻量化的设计模式,在满足各种性能的前提下,利用碳纤维材料得到轻量化的汽车引擎盖。刘浩等[7]通过对汽车引擎盖进行模流分析得到两浇口方案和三浇口方案的充填时间等参数,最终确定了合适的浇口位置。孙开颜等[8]对碳纤维汽车引擎盖的切割加工工艺进行探究,提升了制件的成型质量,满足实际生产要求。黄继峰等[9]对汽车引擎盖的结构进行优化分析,提出多阶段联合优化设计的方法,有效提升了引擎盖的性能。李光霁等[10]对汽车引擎盖进行多目标优化以及可靠性分析,对其轻量化设计进行研究。
本实验通过建立响应面代理模型[11],结合遗传算法对模型进行优化,从而达到减小制件成型变形量、改善制件成型质量的目的。
1模拟仿真1.1建立模型
图1为汽车引擎盖板的三维模型以及二维模型。从图1可以看出,其中制件的长、宽、高分别为453、280、90mm。所用材料为ABS,由于其冲击强度好、耐磨性能优良、热学性能好,因此被广泛应用于汽车内饰部件[12]。
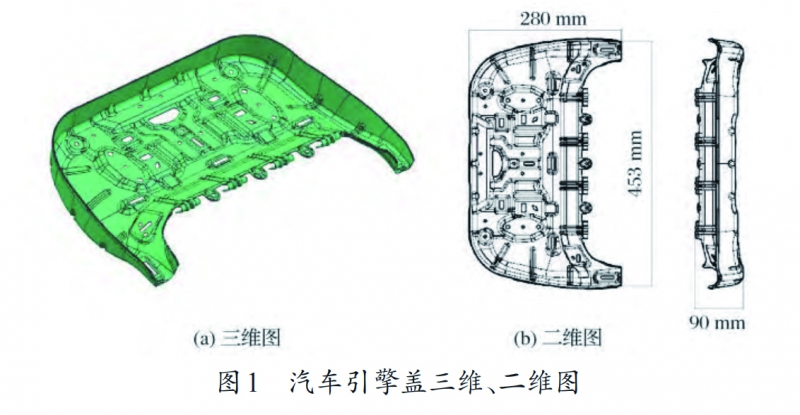
1.2网格划分
利用UGNX三维软件对其进行建模,建立的模型通过Moldflow软件进行分析,首先对其进行网格划分[13]。图2为汽车引擎盖网格网格划分。网格总单元数为40539,最大纵横比为10.52,平均纵横比为1.56,总体满足模拟要求。
1.3初步模流分析
根据实际生产经验,在注塑成型过程中,熔体温度稍高有利于制件成型,这是因为温度高,分子运动快,熔体的流动性能好,但是温度不能过高,温度过高可能导致材料发生热降解,温度过低则可能导致熔体填充不足[14]。模具温度过高会导致熔料粘在模具上,温度过低会导致熔体填充不足[15]。保压压力以及保压时间要适中,过高和过低都会影响制件的成型质量[16]。表1为ABS生产工艺参数。
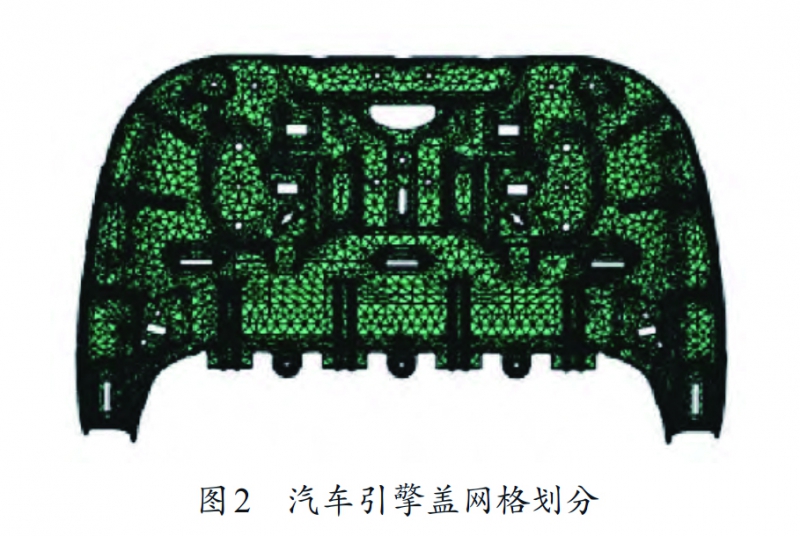
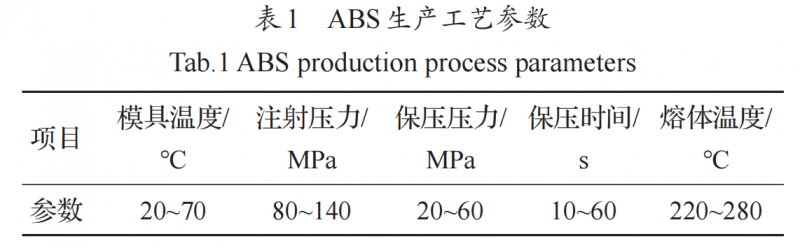
在模具温度为50℃、保压压力为30MPa、保压时间为20s、熔体温度为250℃时,对汽车引擎盖进行初步模流分析,图3为具体结果。
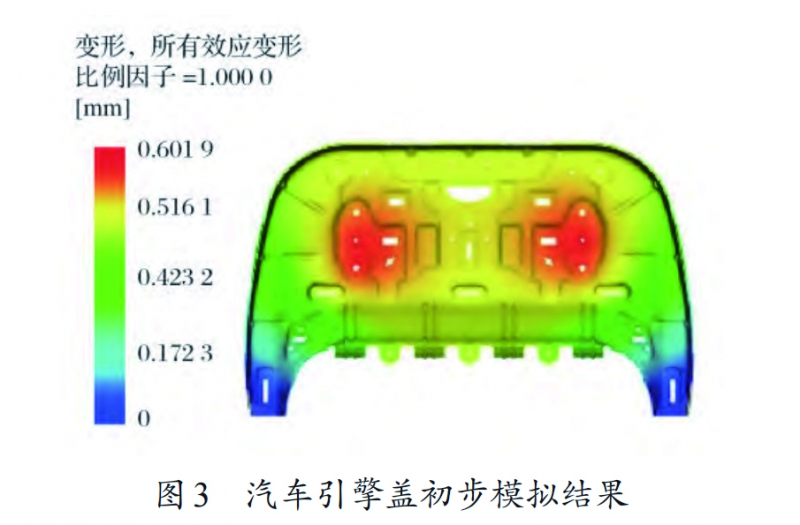
从图3可以看出,汽车引擎盖初步模拟结果最大翘曲变形量为0.6019mm,一般汽车引擎盖翘曲变形量不大于0.5mm,初步模拟结果未满足要求,因此需对其进行优化改进。
2响应面代理模型
响应面代理模型是利用多项式函数拟合设计空间,通过回归模型的选择可拟合复杂的响应关系,具有良好的鲁棒性[17]。本研究通过软件Isight建立响应面代理模型,通过响应面代理模型,可以替代CAE模拟分析,直接预测分析结果[18]。本研究变量为模具温度(A)、熔体温度(B)、保压压力(C)以及保压时间(D),引擎盖的翘曲变形量(R)为研究对象,表2为具体因素水平。根据参数水平随机抽取9组实验样本,表3为响应面代理模型预测结果。
一般通过可决系数来衡量响应面代理模型的优劣程度,可决系数越接近1,表明模型效果越好,当可决系数小于0.9时,模型效果较差,不适合进行后续分析[19]。本次模型可决系数为0.93,大于0.9。图4为可决系数拟合曲线。
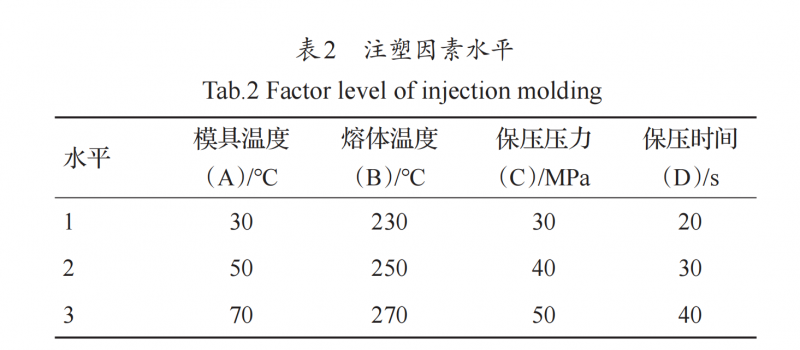
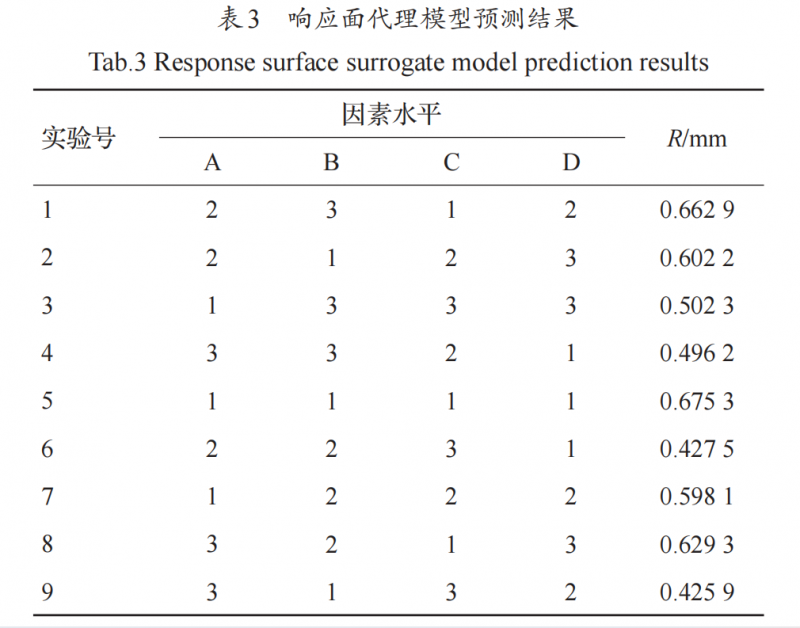
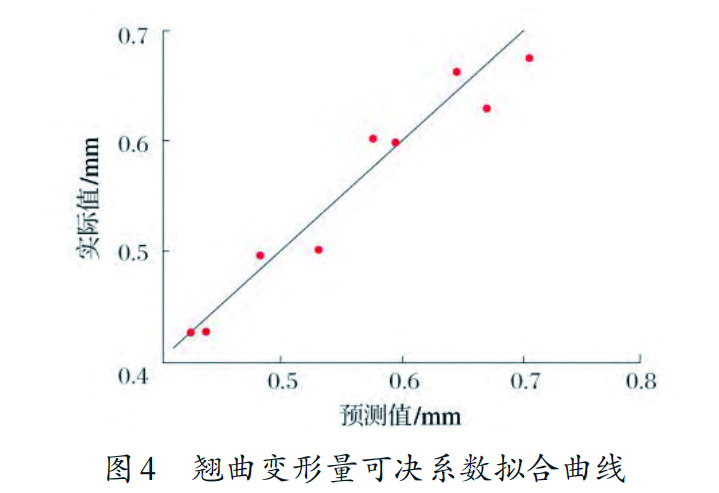
从图4可以看出,响应面代理模型的散点呈现动态分布,这表明拟合效果较好,可以替代CAE分析,提高效率,为后续优化节约时间。
3遗传算法优化
遗传算法是目前应用比较广泛的一种算法[20]。本文通过遗传算法对上述建立的响应面代理模型进行优化,从而得到一组最优解,降低制件生产过程中的翘曲变形量。
一般遗传算法需要确定种群数[21]。本研究所取种群数为12,共设置100组,迭代次数为1200次。图5为4个变量之间的相关性系数。正数表示该因素对结果呈现正相关,负数则表示负相关;相关性系数绝对值越大,表明影响效果越显著[22]。
从图5可以看出,除了熔体温度与翘曲变形量呈正相关外,其余因素与翘曲变形量均呈负相关。各因素对翘曲变形量的影响顺序为:C>B>D>A。
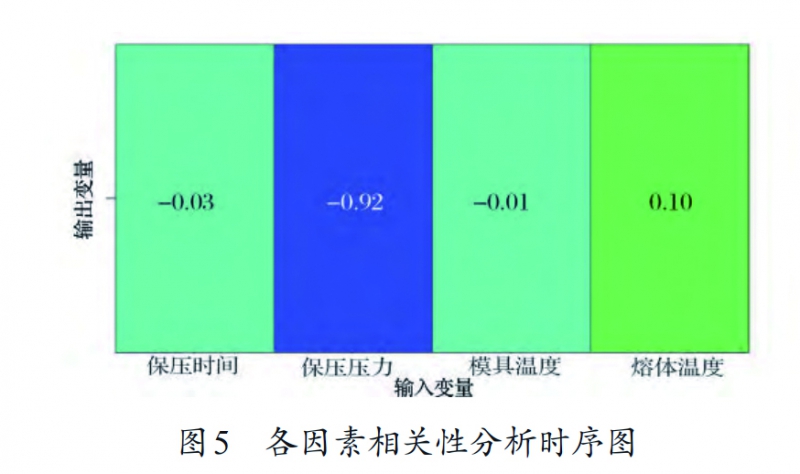
在迭代过程中,直到粒子达到收敛,此时的粒子即为最佳粒子,此时该粒子所在值的大小即为各个因素最终的最优结果[23]。图6为迭代过程粒子分布。
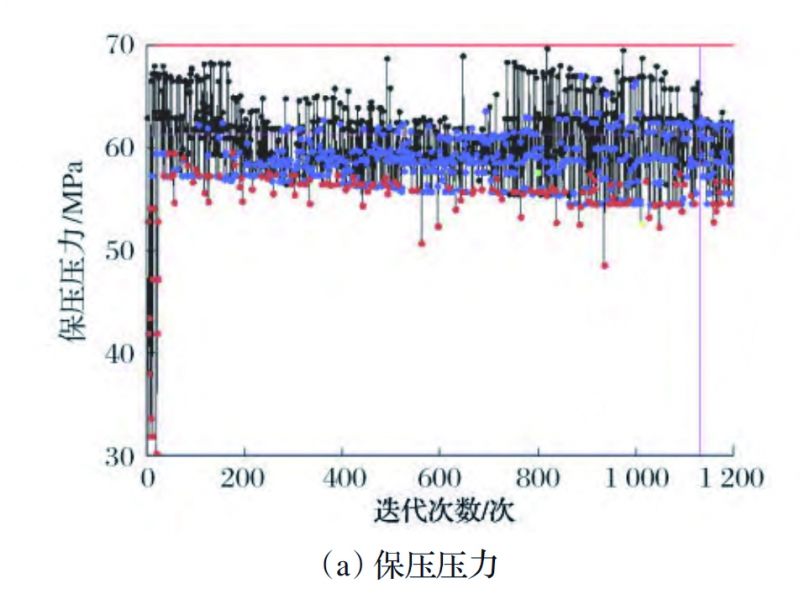
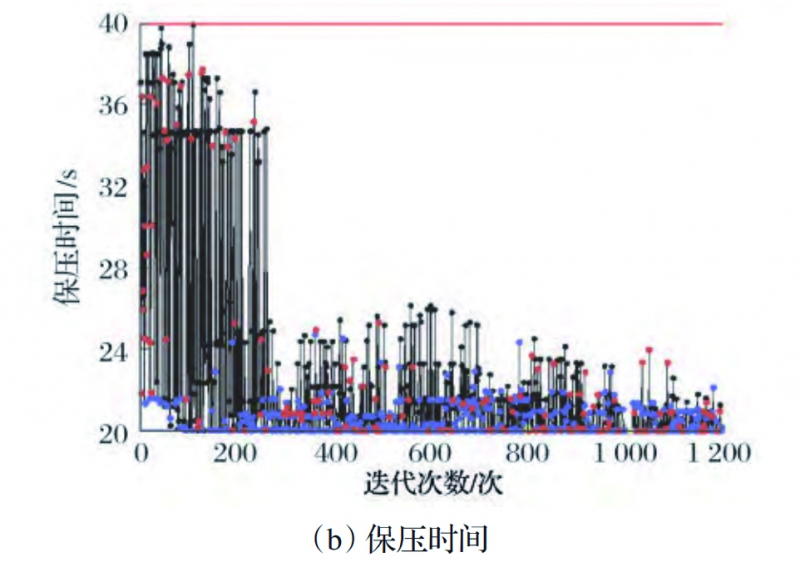
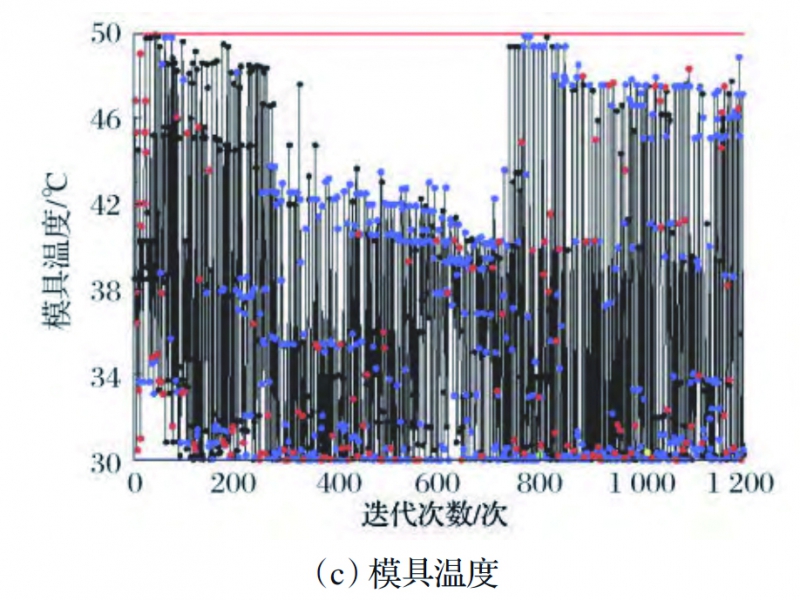
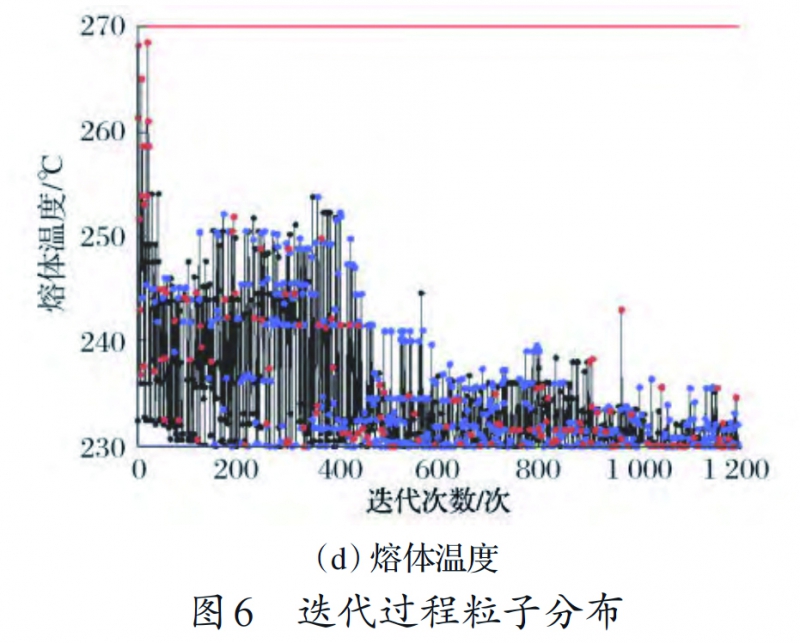
从图6可以看出,当迭代到799次时,粒子达到收敛,该位置处的翘曲变形量最小,即为最终的优化结果,表4为最终优化结果。
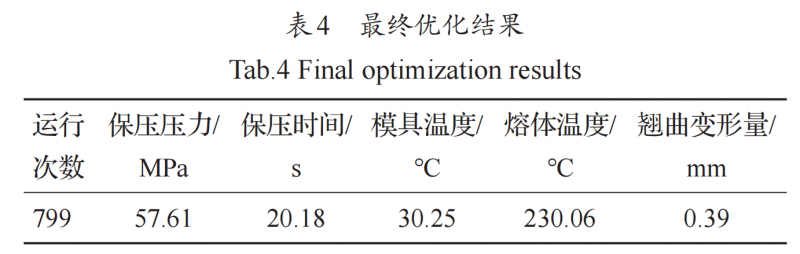
根据上述结果以及实际生产过程,工艺参数均调整为整数,即保压压力为58MPa、保压时间为20s、模具温度为30℃以及熔体温度为230℃时,制件的翘曲变形量最小,为0.40mm。
4模拟验证
当保压压力为58MPa、保压时间为20s、模具温度为30℃以及熔体温度为230℃时,通过Moldflow软件对其进行模流分析,图7为具体的结果。
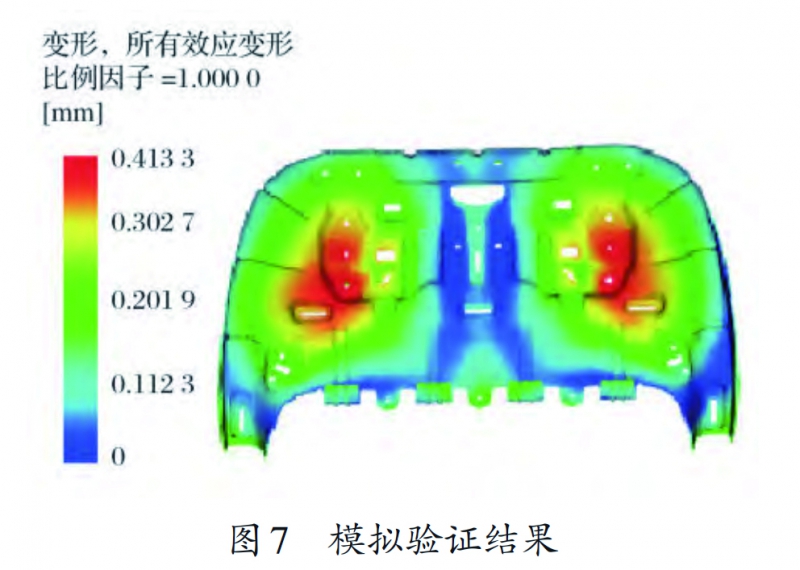
从图7可以看出,制件的最大翘曲变形量为0.4133mm,小于0.5mm,满足生产要求。优化前制件的最大变形量为0.6019mm,两者相差0.1886mm,整体质量提升31.33%。通过遗传算法优化后的预测值为0.40mm,与最终的模拟值相对误差为3.2%,满足要求。
5结论
通过建立响应面代理模型,能够用来预测实验结果,替代CAE分析,提高实验效率。
结合遗传算法对响应面代理模型进行优化,各因素对翘曲变形量的影响顺序为:保压压力>熔体温度>保压时间>模具温度。
当保压压力为58MPa、保压时间为20s、模具温度为30℃以及熔体温度为230℃时,制件的翘曲变形量最小,优化后较优化前减小0.1886mm,整体质量提升31.33%。通过遗传算法优化后的预测值为0.40mm,与最终的模拟值相对误差为3.2%。该方法为后续注塑成型工艺提供一定的参考。
参考文献
[1]方柘林.基于车身结构的轻量化方法研究[D].南昌:南昌大学,2015.
[2]罗婧,廖厚琪,潘梦远,等.丙烯腈-丁二烯-苯乙烯共聚物和聚乙烯的热解特性及动力学[J].武汉工程大学学报,2016,38(1):17-23.
[3]卢惠亲,翟建广,竺宇洋,等.汽车内饰件注塑成型工艺参数的分析与优化[J].农业装备与车辆工程,2022,60(1):138-141.
[4]刘杰,苏玉淋,张亚坤,等.某车型引擎盖模态分析及优化[J].装备制造技术,2023(3):141-144.
[5]李沛,邢彦锋,马振海.基于逆向工程的引擎盖内板法向变形质量分析[J].工具技术,2022,56(5):67-70.
[6]吕玥蒽,陈正国,程超,等.碳纤维复合材料引擎盖的轻量化设计[J].合成纤维,2023,52(6):73-77.
[7]刘浩,陈再良,杨振,等.基于MPI的引擎盖模流分析及工艺优化[J].塑料工业,2019,47(9):52-55.
[8]孙开颜,孙芳兵,张璐,等.碳纤维增强EP复合材料汽车引擎盖切割加工工艺[J].工程塑料应用,2019,47(4):70-74.
[9]黄继峰,周金宇.混杂纤维复合材料汽车引擎盖结构优化设计[J].现代制造工程,2018(4):76-83.
[10]李光霁,刘新玲.引擎盖的多目标优化和可靠性分析[J].现代制造工程,2020(12):19-24.
[11]蒋爱云,张保丰,贾智慧,等.长玻纤增强聚丙烯复合材料注塑成型工艺优化[J].塑料,2020,49(3):85-89.
[12]麻一明,吴剑波,陈宁,等.再生ABS材料的热氧老化性能研究[J].塑料工业,2023,51(4):117-122.
[13]田菲.基于模流分析软件的网格划分和网格修复[J].机械工程师,2018(11):72-74.
[14]颜志勇.PLC控制器塑料端子接口注塑成型工艺参数优化[J].塑料科技,2023,51(5):100-103.
[15]朱红萍,王星星.基于田口实验的水盒盖注塑工艺参数优化与模具设计[J].塑料科技,2022,50(12):80-84.
[16]谭波.ABS自动化设备电子元器件外壳注塑成型工艺优化研究[J].塑料科技,2023,51(6):75-79.
[17]陈川,吕永锋.基于响应面设计及改进NSGA-Ⅱ的变模温注塑成型工艺多目标优化[J].塑料工业,2023,51(6):75-81.
[18]皮卫,熊建武.基于RBF神经网络断路器注塑成型工艺优化[J].塑料科技,2023,51(6):70-74.
[19]王晓衬.基于多目标遗传算法电子适配器成型工艺参数优化[J].塑料科技,2023,51(5):90-94.
[20]刘金娥,刘婉慈.自动化传感器外壳注塑成型工艺优化研究[J].塑料科技,2023,51(5):95-99.
[21]薛茂远,梅益,唐方艳,等.基于GA-ELM及遗传算法的注塑件成型工艺优化[J].塑料,2022,51(1):56-61,66.
[22]钟厉,姚志军,韩西,等.基于遗传算法的碳纤维保险杠注射成型优化[J].塑料,2022,51(5):29-36.
[23]田梦婕,夏勋.注塑工艺对ABS热流道注塑制品翘曲变形的影响[J].现代制造技术与装备,2022(5):175-177.