袁维杰
( 上海工业自动化仪表研究院有限公司,上海 200233)
摘 要:针对吹膜生产工艺无法用穿透式直接对管膜进行厚度测量的问题,利用吹膜生产工艺中旋转卷绕特性,设计了用于管膜在线厚度测量的X射线测厚仪。因穿透式测厚仪是对折叠后上下两层管膜进行厚度测量,而最终结果要求的是单层管膜厚度及对应的挤出模头位置,故希望被测的上下两层厚度一致; 而最有可能保证上下两层薄膜厚度一致的位置是管膜折叠边缘,所以厚度测量点越靠近管膜折叠边缘,所获得的结果越准确。所设计的 C 型结构X射线测厚仪具有测量点跟踪管膜边缘功能,可在不同的吹膜生产设备上安装使用。尤其对管膜折叠卷绕过程中折叠边缘左右移动的情况,该测厚仪能很好地保持测量点在管膜折叠边缘处测量,提升了测量准确度,在实际安装应用中也得到了验证。
关键词: X射线测厚仪;吹膜厚度测量;在线检测;薄膜边缘检测;微处理器
0 引言
薄膜生产的常用工艺有压延法、流延法、拉伸法和吹膜法等[1]。吹膜工艺因其工艺设备简单、薄膜幅宽、没有边废料而得到了广泛应用[2]。目前,吹膜工艺都是用反射式测厚仪直接对圆形管膜上的管壁进行在线测量,而穿透式测厚仪无法直接对管壁进行测量。为解决管壁厚度不均造成收卷时的爆筋现象,吹膜生产工艺所采取的旋转收卷方法,使穿透式测厚仪对管壁实现在线测量成为可能。本文利用吹膜工艺的旋转收卷功能,用穿透式X射线测厚原理,设计了一台可间接对吹膜生产中的管壁厚度进行在线测量的X射线测厚仪。
1 用于吹塑薄膜生产的X射线测厚仪设计
吹膜生产工艺具有旋转收卷特性,即管状薄膜上的每个点都会经过折叠边缘,对折叠薄膜边缘连续测量等同于对管状薄膜旋转测量。根据旋转起始点与模头的对应关系,可以推算出当前测量点显示值(即为对应模头挤出厚度值,这样就可以进行实时在线测量和显示管膜的薄膜厚度)。由于是对折叠后的管膜进行测量,所测得的是两层管膜厚度值,所以,如果折叠的上下两层管膜厚度一致或接近,则测量显示厚度与实际厚度相等。为了减少由于两层膜厚度的偏差可能造成的测量误差,测量点越靠近折叠边缘,测量结果将会越准确。这是因为折叠边缘处上下二层厚度偏差最小。所以对于穿透式X射线测量管膜厚度测厚仪,应能控制测量点在薄膜内且尽量靠近薄膜边缘。
有些吹膜生产设备在收卷膜时薄膜会左右移动,对X射线测量造成很大影响。因此,设计应用于吹膜生产设备的X射线测厚仪时,应使其具备厚度测量、薄膜边缘检测及跟随薄膜边缘移动的功能。
1.1X射线测厚原理
X射线厚度测量是由发射端发射X射线,射线穿过被测介质后由接收探测器测量X射线强度,并通过换算得出被测介质的厚度。计算公式如下:

式中: U为X射线穿过介质后探测到的电压值; U0为发射源与探测器之间只有空气时探测到的电压值; A为常数;μ为被测介质的吸收系数; d为被测介质的厚度。
A和μ是与被测介质相关的2个常数,通过对被测介质的标准样品进行测量获取。当确定了A和μ,并测量得到U0和U值,用式(1) 就可以得到介质的厚度值d[3]。
1.2 硬件设计
整个X射线测厚仪由薄膜厚度测量和薄膜边缘跟随两部分组成。这两部分相对独立,通过一对命令状态线协同工作。
1.2.1 薄膜厚度测量
厚度测量头由X射线管、电离室、微信号放大器、高压电源构成。其将厚度信号转变成电信号,再经信号采集和工控机处理,将薄膜的厚度转换成对应数值,在显示屏上显示[4]。
考虑到有些吹塑薄膜生产设备从折叠到卷绕间距很小,且有些还有倾斜角度,因此要求 X射线测量头尽量小巧,且可以根据倾斜角度进行调整。在选用 X射线发射管时,选择了透射式X射线管。传统的X射线管是将热阴极电子通过高压电场的作用打到阴极靶面上,X射线转换效率不足2% ,大部分功耗变成热能。而透射式X射线管是阳极端靶材直接镀在铍窗内侧,当阴极发射的电子轰击镀在铍窗内侧的靶材时,所产生的X射线可直接透过靶材和铍窗辐射。因此在同样功率条件下,透射靶X射线管要比反射靶X射线管所产生的X射线效率要高且体积小。同样地,在电离室选型上,也是选用了直径仅75 mm 的高灵敏电
离室,并配上微信号放大器构成X射线探测器。由透射式X发射管和X射线探测器,可构成小巧且易于安装的厚度测量头。
厚度测量信号通过信号采集板被工控机读取。同时被读取的还有当前模头位置信号。通过计算得到厚度值和模头号,将连续测量结果显示在操作显示屏幕上,可观察到管膜圆周上的厚度变化曲线。
1.2.2 薄膜边缘跟随
为了保持X射线测量头靠近管膜的折叠边缘,解决部分吹膜生产设备旋转折叠卷绕时薄膜边缘左右移动造成的测量偏差问题,需要有一套既能检测薄膜边缘位置又能使X射线测量头跟随薄膜边缘移动的装置[5]。其必须具备较高的移动响应速度。薄膜边缘跟随模组就是为此而设计的。
薄膜边缘检测模组由激光头、一组光电接受头组成; 通过对光电信号处理,可获取当前薄膜边缘与厚度测量头的相对位置[6]。通过控制步进电机来驱动测量头,可使测量头处在最佳测量位置。
通常管膜是透明的且只有几十微米厚度,因此识别有膜与无膜就是关键。通过各种测试,最后选用一字激光头加一组BPW34 光电管,利用激光穿透薄膜的能量衰减来感知当前测 量点是否有薄膜。虽 然BPW34 响应最灵敏区域在850~950 nm 波长,但为了操作和调整方便还是选择了650 nm 波长。其为可见红光,既能满足薄膜有无检测的需求,又能方便调试和维护。
为了保证X射线测量头保持在尽量靠近管膜折叠边缘且又不使X射线测量头频繁来回移动,需要检测到薄膜边缘与X射线测量头相对位置,超出偏差范围需及时调整。因此,必须知道薄膜边缘在检测区域中的位置。因为需要检测一个区域,故选用一字型激光头5个 BPW34光电二极管构成区域检测。薄膜边缘检测如图1所示。
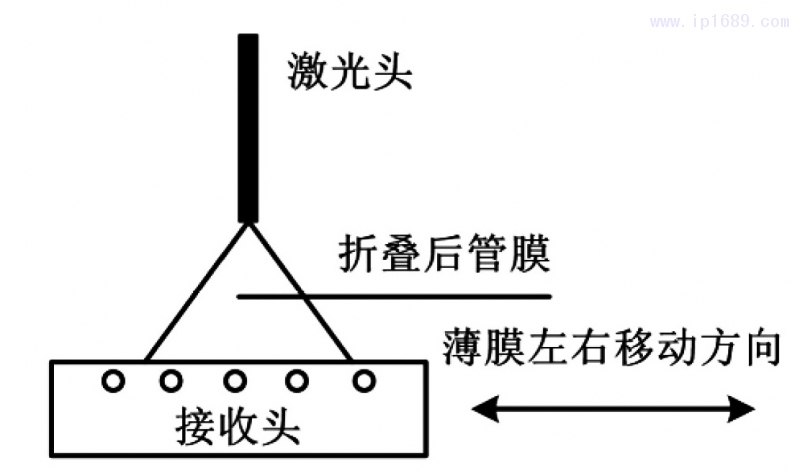
图1 薄膜边缘检测示意图
薄膜边缘位置以中间检测点为基准,通过中间点状态检测来控制X射线测量头移动方向及到位停止。
为便于跟随模组的运行诊断,模块内部安装OLED显示器,可显示当前工作状态、与测厚程序的间接口状态信息、驱动输出控制信息、薄膜边缘检测信息、系统异常时的故障码等,有故障或需要读取时点亮,正常状态下会自动关闭。
薄膜边缘检测模组运行模式切换到手动状态时,可以手动控制检测头移动和标定被测薄膜。通过标定,可以解决激光头衰减、光电器件老化、薄膜品种变更等因素造成的检测异常等问题。
1.2.3X射线测厚仪功能框图
X射线测厚仪电路功能框图如图2所示。虚线框内的硬件模块、电路安装在操作控制箱内,可安装在便于监控操作的位置; 其余部分安装在C型扫描架上,需安装在收卷检测薄膜位置。

图2 X射线测厚仪电路功能框图
1. 3 结构设计
为了适应不同的机器安装,将X射线测量头设计成可调结构。C型扫描结构如图 3 所示。
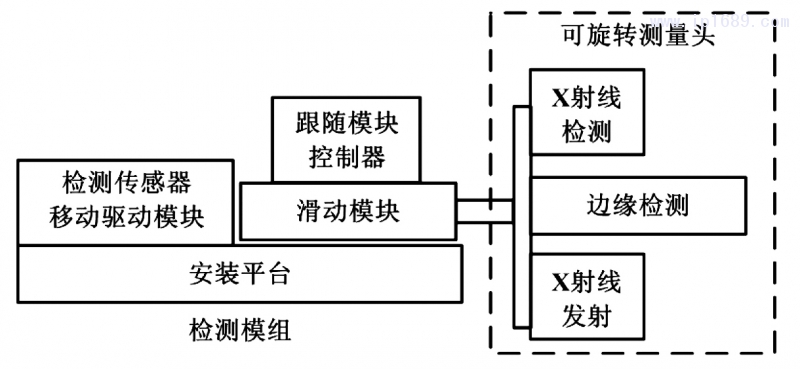
图3 C型扫描架结构图
模组的安装平台是固定在吹膜生产设备上的,可旋转测量头悬挂在安装平台的滑动模组上。改变悬挂角度,可使X射线与被测薄膜保持垂直,提高测量精度和稳定性,达到最佳测量效果。可旋转测量头下部安装的X射线发射管和安装在上部的X射线探测器构成了测量回路。通过调整X射线发射管位置,可调节测量间隙,满足不同工况条件需求。在X射线测量回路侧面安装了薄膜边缘检测头,检测被测薄膜是否处在测量回路中。
安装平台上的滑动模块由步进马达带动,由滑动模块再带动可旋转测量头移动。也就是说,X 射线测量回路可通过控制步进马达使测量点左右移动。为了防止滑动模块超出移动范围,对步进电机及驱动电路进行保护,在滑台左右两端安装了限位接近开关。基于模组的外形及体积上的要求,选用的步进电机功率较小,以能驱动滑台为准; 通过对步进电机升降时序控制,可解决快速移动滑台需求[7-8]。
如果在收卷前位置对薄膜测量,则安装平台可固定在收卷辊侧板上。滑台的滑动距离根据生产品种和实际工况条件进行选择。考虑到滑块负重,一般选择滑台移动距离在400 cm 以内。
1.4 软件设计
整个测厚仪软件由两部分构成: 基于Windows 的采用C语言和VB.net 开发的厚度测量显示软件和基于STM 平台用C语言开发的薄膜边缘跟踪控制软件。
1.4.1X射线厚度测量软件设计
厚度测量程序是这个X射线测厚仪的主控程序,用于实现人机操控界面、测量数据采集、数据处理、监控跟随系统及监控和处理测厚仪运行状态等功能。X射线测厚仪软件流程如图 4 所示。
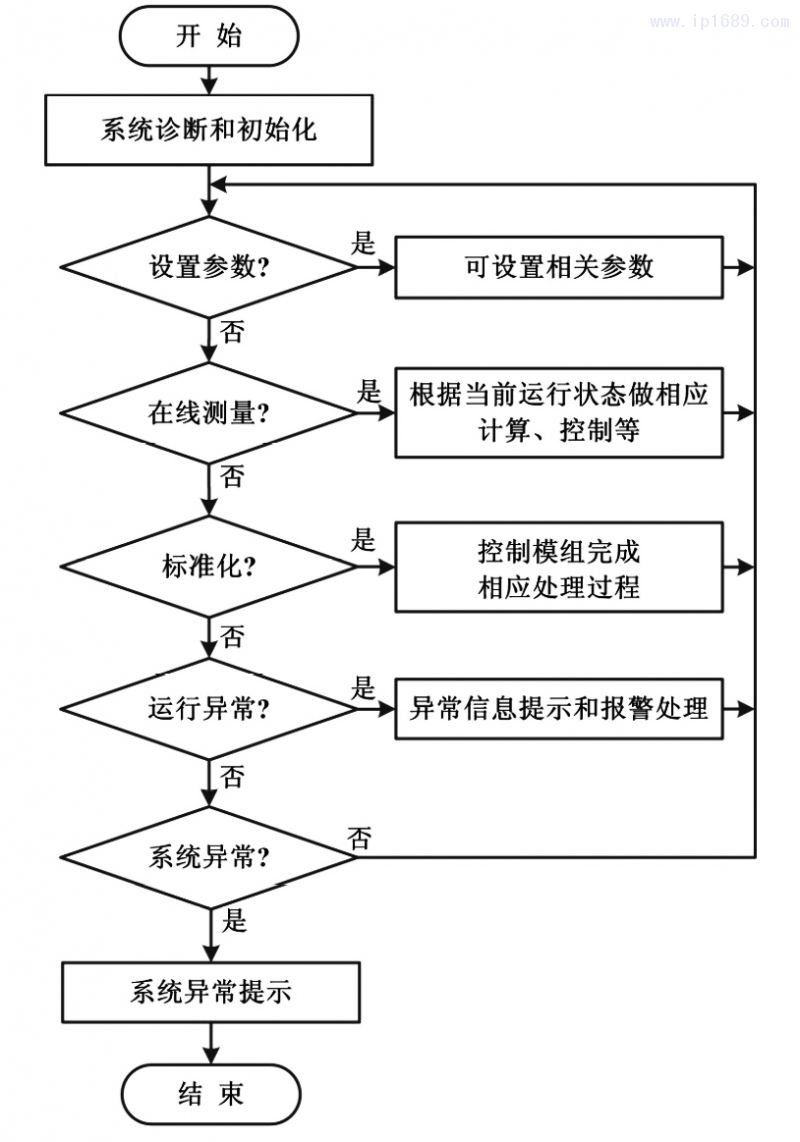
图4 X射线测厚仪软件流程图
1.4.2 X射线探测头标准化处理
X射线运行一段时间后,随着时间和温度的变化,U0也会发生变化。根据厚度计算公式(1),U0的变化将影响计算后的厚度值。为了保证测量准确,需要不断监测U0 的变化。标准化处理就是对U0 的监测处理[9]。通常,标准化处理周期是按实际使用环境来设置为定时自动处理,但也可按需要进行手动处理。按U0定义就是X射线探测头在没有介质的状态下测得的电压值,标准化就是将X射线测量头移到没有被测
介质遮挡的位置读取电压值。
标准化处理过程: 当到达设定的时间或扫描次数后,测厚程序发命令给跟随模组; 模组收到命令后控制滑台回到起始位置,到位后输出完成状态; 测厚程序收到到位信息后开始读取、计算、处理和更新U0,完成后重新进入启动测量过程。
1.4.3 薄膜边缘跟随软件设计
跟随模块选用STM8 微处理器为控制器,处理薄膜边缘信号检测、控制驱动X射线测量头跟随薄膜移动、与测厚程序同步工作、显示当前工作状态信息等,可对薄膜检测头进行标定,并可手动操控滑台移动。跟随控制程序流程如图5所示。
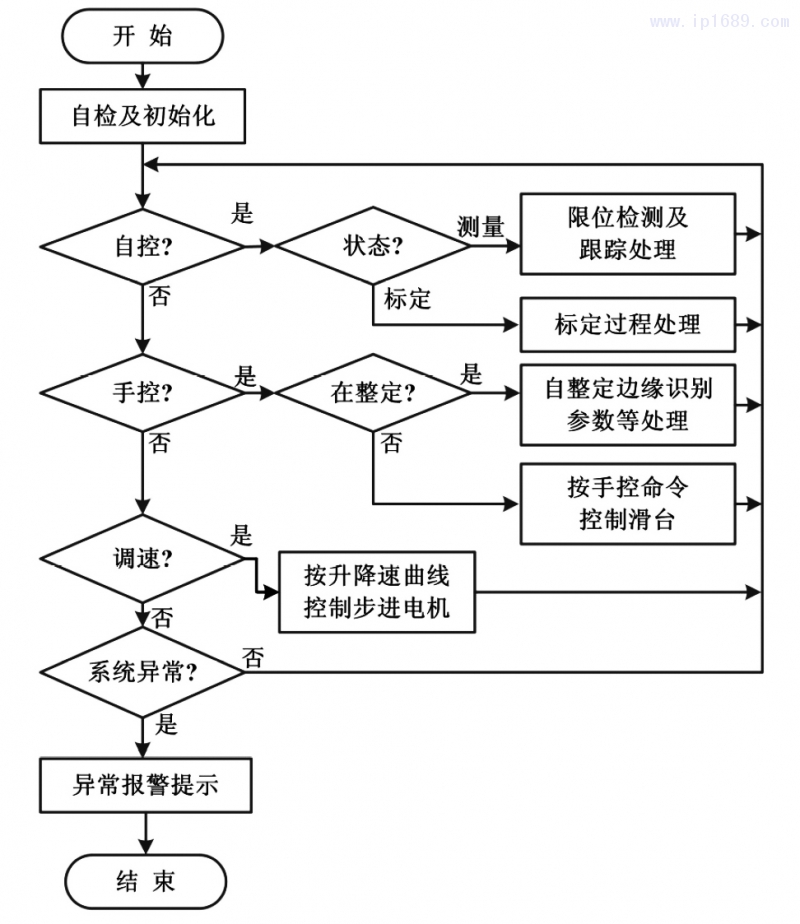
图5 跟随控制程序流程图
当跟随模块初始化完成且设置在自动状态时,跟随模块将接收测厚程序控制,完成薄膜边缘跟随和U0标定工作; 如果跟随模块设置为手动状态,则可以手动控制滑台移动或进入薄膜边缘检测标定操作。标定操作是通过长按标定按钮与状态指示反馈来显示操作所处步骤,标定操作需完成读取无膜、有膜阈值并计算处理和保存等。标定过程中,可通过切换到自动状态来终止标定工作。
2 X射线测厚仪应用结果
目前,根据用户的吹膜生产设备及生产的产品类型,制作了适用于该吹膜生产设备的 C 型X射线测厚仪。该设备生产的是热缩膜,有多种规格,厚度为15~25μm、宽度为1.6 ~ 1.8 m。根据实际生产时薄膜晃动情况,将X射线测量头间距设置为20 mm,选用最大行程为300 mm 滑台可满足不同产品宽度及薄膜偏移的 需 求。X射线测量点直径10 mm,测量精 度在±1μm内,测量中心点与薄膜边缘间距15 mm,允许测量偏离范围在±5 mm内,跟随响应时间在0.5 s内。
在安装了X射线测厚仪的生产设备上,操作员可以实时看到当前的产品厚度及均匀度,并及时调整模头间隙,以提高产品的质量并能降低产品成本。尤其是更换生产品种时,对于设备的调整给予很大帮助,可减少调整时间和调整时所耗费的原材料。
X射线测厚仪小巧且安装简单,现已有多套安装在该类吹膜设备上运行。因采用的是低能X射线,所以在安全上属于免检产品,比起使用放射源的反射式测厚仪,管理成本更低也更安全。
3 结束语
本文设计了适用于吹塑薄膜生产的X射线测厚仪,解决了吹膜生产工艺中使用穿透式测厚仪来测量管膜厚度存在的两个问题。①厚度测量点要保持在管膜折叠处,这样上下两层薄膜厚度相对一致,可保证测量精度。②厚度测量点位置与吹膜模头要有确切的对应关系,这样厚度测量值可正确对应到模头位置,便于调整模头使生产的薄膜厚度均匀提升产品质量。该测厚仪具备测量点跟踪管膜边缘功能,具有广阔的应用前景。
参考文献:
[1]敏隆叶,埃贝尔.塑料薄膜加工技术[M].王建伟,孙小青,左秀琴,译.北京: 化学工业出版社,2003.
[2]张玉霞.吹塑薄膜技术进展[J].塑料包装,2007,17( 3) : 38-46.
[3]靳其兵,吴磊. 有关X射线测厚仪技术的研究[J].自动化仪表,2007,28( 1) : 65-66.
[4]张晓春.X射线测厚仪在热轧板带中的应用[J].自动化仪表,2014,35( 2) : 88-91.
[5] 薛晓旭. 基于单片机的透射式光电纠偏检测装置的制作[J]. 广东印刷,2013( 3) : 41-43.
[6] 章佳辉,郭华亮,徐志宇,等. 用于超级黑板的可抗震型光电定位系统设计[J]. 自动化仪表,2017,38( 8) : 9-13.
[7] 仪慧玲,张仁杰. 基于 STM32 的步进电机 S 曲线加减速算法的 优化[J]. 信息技术,2015( 3) : 178-181.
[8] 王粟,张威亚,常雨芳. 步进电机控制器在液晶屏压合器中的应 用[J]. 自动化仪表,2016,37( 8) : 30-33.
[9] 魏运鹏,方伟. X 射线测厚仪测量精度影响因素及补偿措 施[J]. 自动化仪表,2011,32( 10) : 79-81.