刘祥建,周佳睿,姜劲
(金陵科技学院机电工程学院,南京211169)
摘要:针对某种塑料按钮开关帽带有环形侧凹且帽体壁厚变化不均匀的结构特点,设计了一套带斜导柱侧抽芯机构的一模两腔模具。为改善塑件质量及解决塑件脱模问题,首先,结合Moldflow软件仿真确定了浇口位置和冷却系统,并对塑件的成型过程进行仿真分析,结果显示,塑料熔体充满型腔的时间短且两型腔的充型一致性好,同时,塑件的体积收缩率小且两型腔内的塑件体积变化均匀,型腔内气体的排出情况较好,气穴少,塑件产生的翘曲变形量在合理变形范围之内。其次,对模具结构进行设计,主要包括分型面、成型零件以及侧抽芯机构。由于塑件带有环形侧凹,型芯设计成组合式结构,并由大型芯、滑块和成型杆成型塑件的帽体部分,采用斜导柱侧抽芯机构实现塑件环形侧凹的成型并脱模。通过Moldflow软件分析和优化模具设计方案,可以加快模具的设计过程,提高塑件的成型质量。
关键词:按钮开关帽;注塑模具;浇口位置;成型过程
随着我国经济的不断发展,塑料制品因成本低、质量轻、力学性能相对较高等诸多优点,在车辆制造、家用电器、医疗器械等领域得到了更为广泛的应用。与此同时,注塑模具作为塑料制品成型的主要设备,其设计与制造技术也在快速提升[1-6]。
CAD/CAE计算机辅助技术的应用大大方便了注塑模具的设计过程,为生产出更低成本、更高质量的塑料制品提供了帮助[7-11]。王巍等[12]设计了机载计算机卡钩塑件的注塑模具,并应用Moldflow软件对塑件的浇口位置和成型过程进行了仿真模拟,设计过程中,根据仿真模拟结果选取了塑件的最终浇口位置,塑件的成型分析结果显示塑件浇口位置的设置是合理的。吴小飞[13]进行了扫地机器人底座塑件的注塑模具设计,针对设计的注塑模具结构,应用Moldflow软件对浇注系统和冷却系统设计的合理性进行了仿真验证。邵良臣等[14]进行了汽车控制面板旋钮开关注塑模具结构的设计,并运用Moldflow软件进行了塑件成型过程中的流动、冷却及翘曲仿真模拟,从而对塑件的成型工艺方案进行优化。耿金萍等[15]设计了偏心轮支架塑件的注塑模具,设计过程中,为获得最佳浇口位置,保证塑件制品的成型质量,运用Moldflow软件对设计的浇注系统进行了仿真分析。熊江等[16]应用UG软件进行了塑料散热板格栅热流道叠层注塑模具的结构设计,并运用Moldflow软件进行了最佳浇口位置仿真和浇注系统充填工艺性仿真,优化了注塑工艺方案。可以看出,Moldflow软件在优化注塑模具设计结构、验证模具结构的合理性方面发挥了作用,通过仿真模拟有利于降低模具的试模成本、加快模具设计过程、提升塑件制品的质量。
笔者以某种塑料按钮开关帽为对象进行注塑模具设计,按钮开关帽带有环形侧凹且帽体壁厚变化不均匀,为改善塑件质量及解决塑件脱模问题,应用Moldflow软件对塑件的浇口位置和成型过程进行仿真分析并优化模具设计结构,得到合理的注塑方案。
1 塑件分析
按钮开关帽结构如图1所示,整体外形呈中心对称结构,上部为帽盖部分,下部为帽体,塑件结构主要由平面、圆弧面组成,其中,帽盖部分与帽体之间形成环形侧凹。塑件外形尺寸为50mm×50mm,最大壁厚为6mm,最小壁厚为1.5mm。塑件材料为丙烯腈-丁二烯-苯乙烯塑料(ABS),其密度为1.05g/cm3,收缩率为0.4%~0.7%,该材料耐磨性优良,尺寸稳定性好,且冲击强度较好,在机电产品中应用广泛。
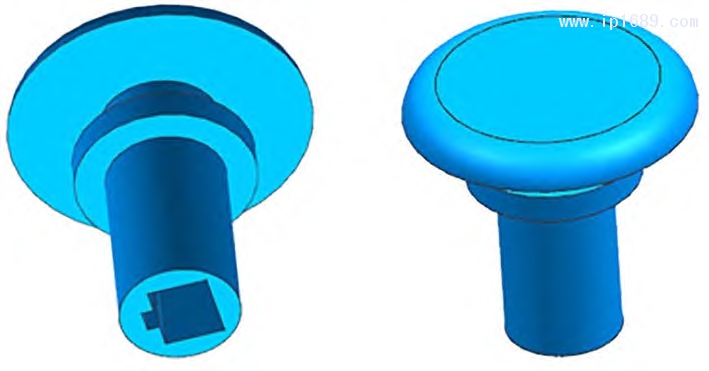
图1按钮开关帽结构示意图
使用UG软件中的体积测量功能,得出塑件的体积约为20.40cm3,塑件的质量约为21.42g。
2 塑件成型工艺分析
2.1 网格划分
为提高注塑模具结构的合理性,在进行模具设计之前应用Moldflow软件对塑件的浇口位置和成型过程进行仿真分析。建立按钮开关帽仿真模型,并进行网格划分,网格划分后共得到10150个三角形单元,网格质量的匹配百分比为80%,网格划分结果如图2所示。
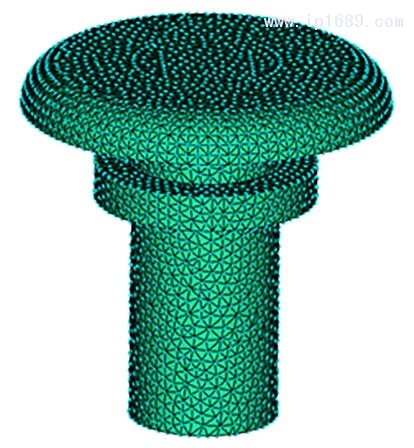
图2 网格划分结果
2.2 浇注系统方案
浇注系统决定了塑料熔体在注塑模具中的运动流向,合理的浇注系统结构可以保证来自注塑机喷嘴的塑料熔体达到最佳的流动状态,并实现平稳、顺利地充模,完成整个浇注过程。考虑到塑件制品的结构尺寸较小及塑料熔体流动过程中的流动平衡、压力平衡的影响,为提高生产效率及确保塑件质量的均匀和稳定,注塑模具采用一模两腔结构,型腔排布采用平衡式排列。
浇口的位置对塑件质量影响较大,为此,利用Moldflow软件对塑件进行浇口位置分析,仿真结果如图3所示。可以看到,推荐的比较合适的浇口位置在邻近环状凸起的塑件帽体一侧附近,考虑到塑件的环状凸起结构以及塑料熔体的流动阻力的影响,将浇口选在环状凸起靠近塑件帽体的边沿位置。
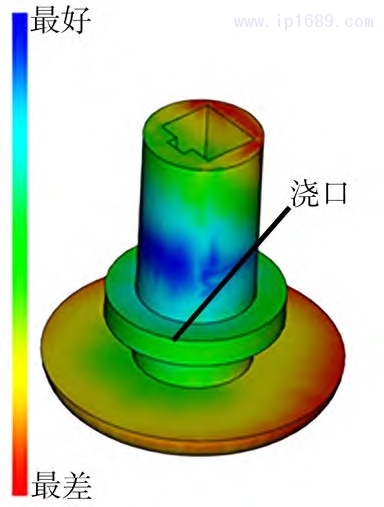
图3 浇口位置仿真结果
根据上述分析结果,浇口选用侧浇口形式,并设计浇口厚度为0.8mm,宽度为2mm,长度为2mm;主流道为圆锥形结构,设计其小端直径为5mm,大端直径为8.24mm,长度为92.7mm,球面凹坑半径为20mm;分流道为圆形截面结构,设计其直径为6mm。
2.3 冷却系统方案
塑料熔体在注塑模具中冷却成型时,其温度的变化过程会直接影响塑件质量的优劣以及塑件生产效率。如果温度控制不好,塑件容易产生翘曲变形、应力开裂、表面不光泽及熔合纹等,造成塑件品质下降,甚至不合格。同时,塑料熔体的冷却时间是影响生产效率的关键因素。
注塑模具常使用循环水进行冷却,其中,冷却回路的形式和冷却管道的直径是冷却系统设计考虑的两个主要内容。为减小出入水的温度差异,使用常温水作为循环水进行冷却,冷却水管上、下各有两根,且以环绕塑件四周的结构形式进行布局,其中,冷却水管直径为10mm,冷却水管布局如图4所示。
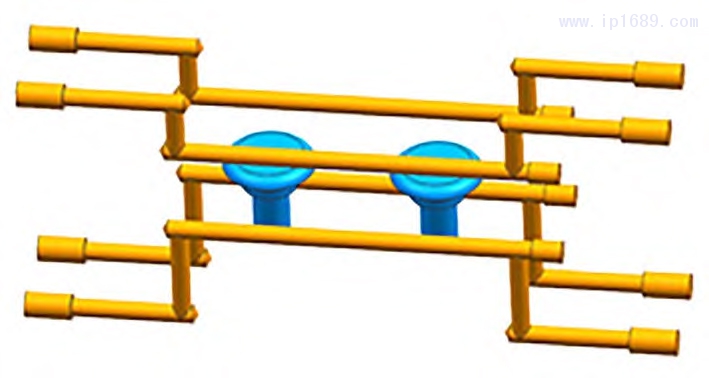
图4 冷水管布局示意图
2.4 成型分析结果
根据前述的浇注系统方案和冷却系统方案,利用Moldflow软件模拟塑件的成型过程,对影响塑件成型质量的填充时间、体积收缩率、气穴位置、翘曲变形量等因素进行分析。在仿真模拟过程中,设置塑料熔体温度为240℃,保压时间为10s,开模时间为5s。
图5为填充时间仿真结果。从图5可以看出,塑料熔体充满型腔的时间为0.6359s,可短时间内将塑料熔体充满型腔,同时,在填充过程中,塑料熔体流至两型腔末端时间的一致性好,且流动均匀平稳,没有出现填充不足的情况,因此,有利于获得高精度、密实的塑件。
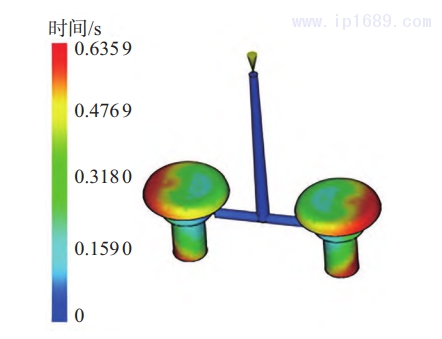
图5 填充时间仿真结果
图6是体积收缩率仿真结果。从图6塑件的体积变化情况可以看出,两型腔内的塑件体积变化均匀,且体积收缩率小,未出现局部位置体积收缩率较大的缺陷,塑件的尺寸稳定性较好。
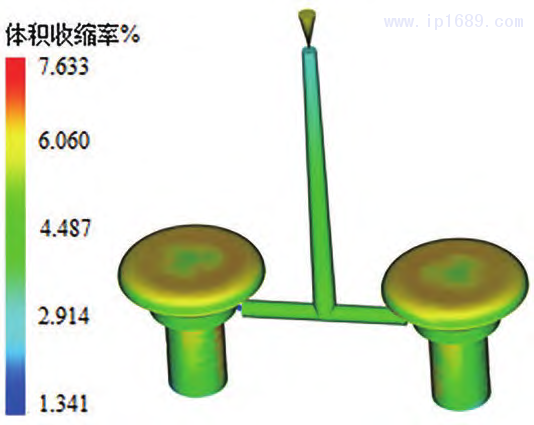
图6 体积收缩率仿真结果
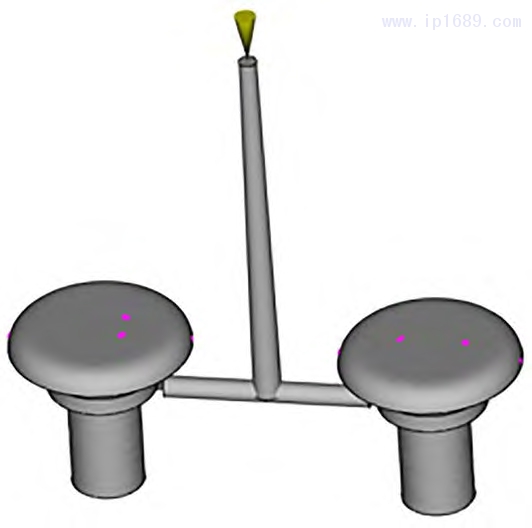
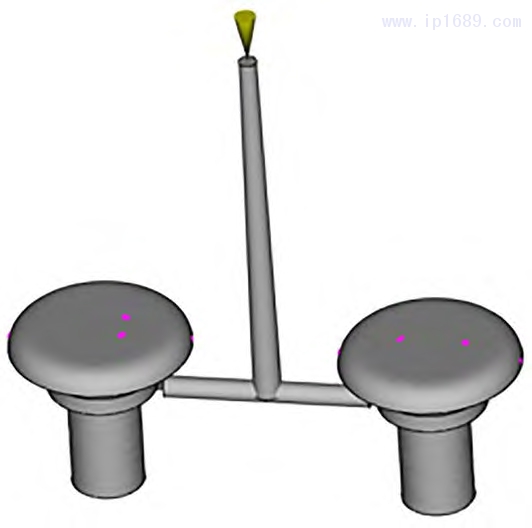
图7是气穴分布仿真结果
从图7可以看出,只在塑件帽盖部分表面产生了几处气穴现象,说明型腔内气体的排出情况较好,另外,气穴相对接近帽盖部分的边沿,位置靠近分型面,而且该塑件的体积较小,排气量较小,可利用注塑模具分型面之间的微小间隙自然排气,更有利于型腔内气体的排出,避免气穴的产生。
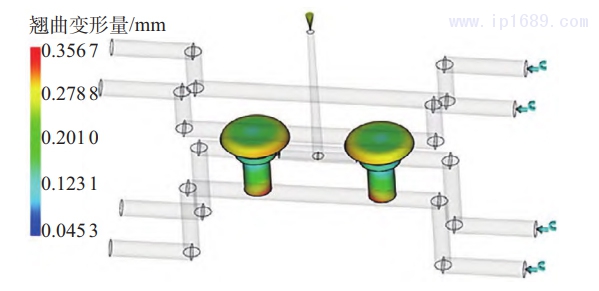
图8是翘曲变形量仿真结果。
从图8可以看出,塑件的翘曲变形主要发生在帽盖部分上部和帽体部分下部,这两处位置由于塑件形状结构的原因,壁厚变化不均匀,导致塑件收缩不均匀而发生翘曲变形,其中,产生的最大翘曲变形量为0.3567mm,相对塑件的结构尺寸,该变形量在合理变形范围之内,能够保证塑件的成型精度。
综上所述,前述注塑模具的设计方案能够满足成型要求。
3 模具结构设计
3.1 分型面设计
分型面选择的优劣将直接影响到塑件的成型质量,以及模具结构的复杂程度、注塑工艺操作的难易程度。
根据分型面位置的选择原则,该塑件分型面的设计,应满足以下要求:(1)因为该塑件的外观面要求光顺,因此,分型面要尽量避免选择在塑件光顺的外表面位置处;(2)因为注塑模具的推出机构一般设在动模部分,因此,分型面的选择要尽量保证塑件能留在动模部分;(3)因为该塑件的外表面存在环形侧凹,需要设计侧抽芯机构实现脱模,因此,分型面的选择要尽量使侧抽芯行程较短。
综合上述选择要求,分型面选择在帽盖部分与环形侧凹结合处的最大截面位置,如图9所示。
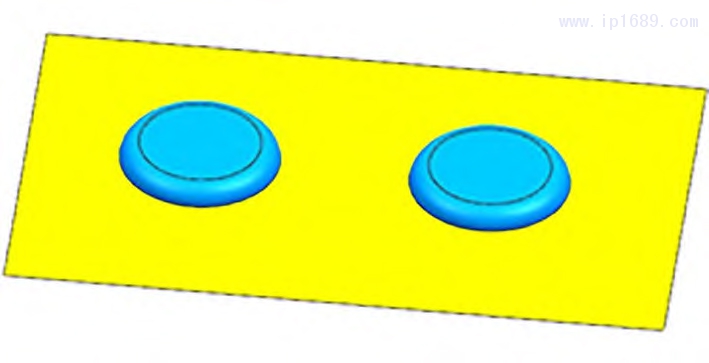
图9 分型面示意图
3.2 成型零件设计
成型零件包括型腔和型芯,注塑过程中,型腔用于成型塑件的帽盖部分,型芯用于成型塑件的帽体部分。
常见的型腔结构有整体式、组合式两种形式。该塑料按钮开关帽尺寸较小,帽盖部分结构简单,因此,注塑模具型腔采用整体式结构,其结构如图10所示。
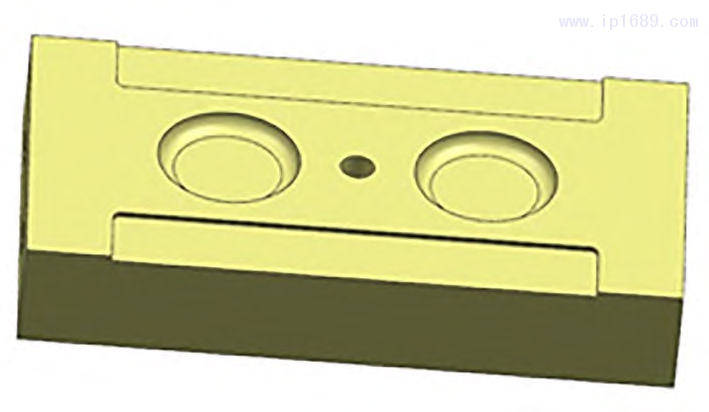
图10 型腔结构示意图
型芯也有整体式、组合式两种结构形式,整体式型芯常用于小型的塑件,较大塑件的注塑常采用组合式型芯。设计过程中,考虑到帽体部分的环形侧凹结构和孔状结构,型芯采用组合式结构,由大型芯和滑块成型帽体的环形侧凹结构,由成型杆成型帽体的孔状结构。其中,大型芯的结构如图11所示。
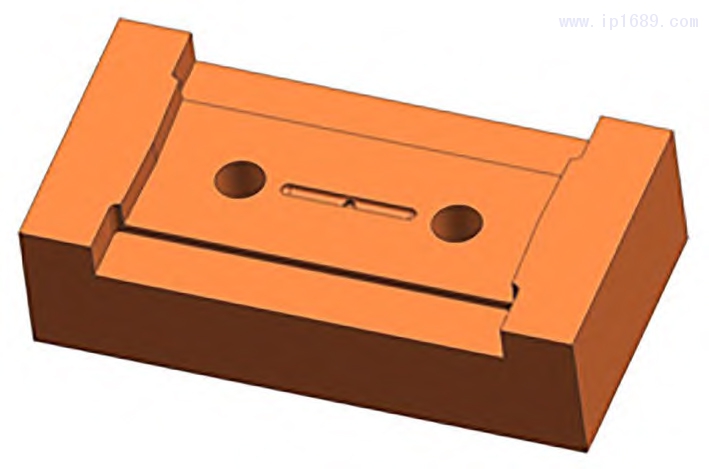
图11 大型芯结构示意图
3.3 侧抽芯机构设计
由于该塑料按钮开关帽的帽盖部分与帽体之间形成环形侧凹,具有与开模方向不一致的分型,注塑模具开模时无法直接将塑件推出,因此,设计过程中,需要考虑注塑模具的侧向分型与抽芯。
该塑件环形侧凹较浅,抽芯距较小,因此采用斜导柱抽芯机构,在结构形式上,将其设计成斜导柱安装在定模上、滑块安装在动模上的形式。这种结构形式适合于塑件的外侧抽芯,开模过程中,通过斜导柱驱动侧面的滑块向外运动,从而方便推管将塑件从成型杆上推出。
3.4 模具整体结构及工作过程
该塑料按钮开关帽的注塑模具整体结构如图12所示。注塑模具的工作过程如下所示。
(1)合模过程。动模与定模进行合模,在注塑机合模机构推动下,通过导柱的导向,动模向定模方向运动,实现注塑模具的合模并锁紧。
(2)注塑过程。塑料原材料在注塑机的料筒内被加热至熔融状态,然后塑料熔体通过注塑机的喷嘴依次进入注塑模具的主流道、分流道、浇口,最后进入型腔。
(3)保压和冷却过程。塑料熔体在注塑模具的型腔内进行保压和冷却,进而获得相应形状的塑件。
(4)开模过程。在注塑机的开模力作用下,动模向远离定模的方向运动,动模与定模在分型面位置分开一定的距离,在动模运动过程中,主流道里面的塑料凝料将脱离定模并跟随动模一起运动,同时,在斜导柱的驱动作用下,滑块相对于塑件向外运动,实现注塑模具的侧向分型与抽芯,注塑机推动推板,进而推管将塑件从成型杆上推出掉落。
(5)复位过程。动模与定模再次进行合模,继续进行下一个周期的注塑工作过程。
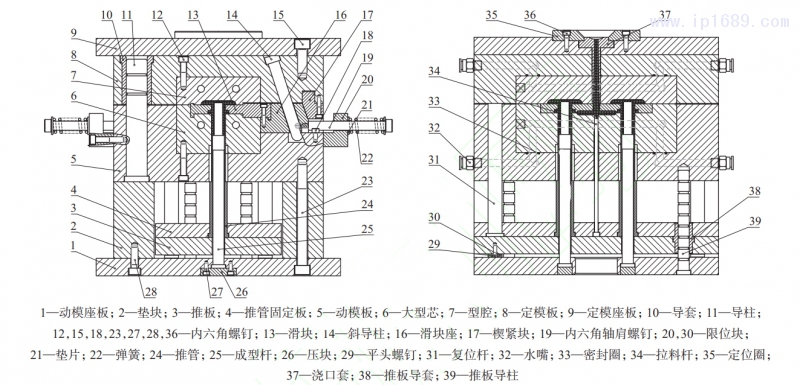
图12 注塑模具结构图
4 结语
开关件在机电产品中应用广泛,以某种塑料按钮开关帽为对象应用Moldflow软件对其浇口位置和成型过程进行仿真分析,并完成了塑件的注塑模具结构设计。主要分析结果和设计工作如下所示。
(1)通过浇口位置仿真分析,浇口设计为侧浇口形式且位于环状凸起靠近塑件帽体的边沿位置处。塑料熔体的成型仿真结果显示,塑料熔体充满型腔的时间为0.6359s,充型时间短且两型腔的充型一致性好;塑件的体积收缩率小,两型腔内的塑件体积变化均匀,未出现局部位置体积收缩率较大的缺陷;塑件的气穴少且位置相对接近帽盖部分的边沿,型腔内气体的排出情况较好;塑件产生的最大翘曲变形量为0.3567mm,变形量在合理变形范围之内。
(2)注塑模具设计为一模两腔的结构形式,结合塑件的结构特点,分型面选择在塑件帽盖部分与环形侧凹结合处的最大截面位置,型腔设计成整体式结构,型芯设计成组合式结构,并由大型芯、滑块和成型杆成型塑件的帽体部分,采用斜导柱侧抽芯机构实现塑件环形侧凹的成型。
参考文献
[1]胡开元,李虹波,王雷刚.汽车手套箱外盖注塑模具设计[J].工程塑料应用,2022,50(3):101‒105.
[2]孙令真,叶烁.分体空调底盘注塑模具设计[J].中国塑料,2021,35(12):129‒136.
[3]陈亚梅.电动车后视镜连接头注塑模具设计[J].合成树脂及塑料,2021,38(6):50‒54.
[4]周建安.行车记录仪面壳注塑模具设计[J].中国塑料,2021,35(11):133‒137.
[5]徐自明.某医疗器械带金属嵌件塑件的注塑模具设计[J].合成树脂及塑料,2021,38(2):62‒66.
[6]毛金明,马野.厨卫处理机壳体注塑模具设计[J].模具技术,2021(6):13‒18.
[7]聂勇军,刘志军,唐振宇.基于CAD/CAM的磁电式振动传感器注塑模具设计[J].塑料科技,2021,49(6):84‒86.
[8]朱彦,徐乔擎,庄向斌.基于Moldflow的遥控器壳精密注塑模具设计[J].塑料科技,2021,49(3):70‒72.
[9]王平洲,钟丽霞,郑志军,等.基于Moldflow和UG的杯托注塑模设计[J].工程塑料应用,2022,50(7):99‒103.
[10]汪政,冯文,孙袁星.基于Moldflow的揭盖式洗发水瓶盖注塑模具设计[J].工程塑料应用,2022,50(6):105‒110.
[11]徐兰英,冯思晨,叶帼珊.基于Moldflow的滑动开门钩注塑模具设计[J].广东技术师范大学学报,2022(3):8‒14.
[12]王巍,张贺,李珍.机载计算机卡钩注塑模具设计[J].塑料,2022,51(2):43‒46.
[13]吴小飞.扫地机器人底座注塑模具设计[J].机电信息,2022(4):48‒50.
[14]邵良臣,王悦,张鹏玉,等.基于Moldflow的汽车控制面板旋钮开关注塑模具设计[J].塑料工业,2019,47(5):67‒71.
[15]耿金萍,郭永环,顾祎乙,等.偏心轮支架注塑模具设计研究[J].装备制造技术,2021(3):131‒135.
[16]熊江,易良培.基于UG和Moldflow的散热板格栅热流道叠层注塑模具设计[J].机械工程师,2021(5):102‒104.